AI-Driven Inspection Fuels Meat Processors for Success
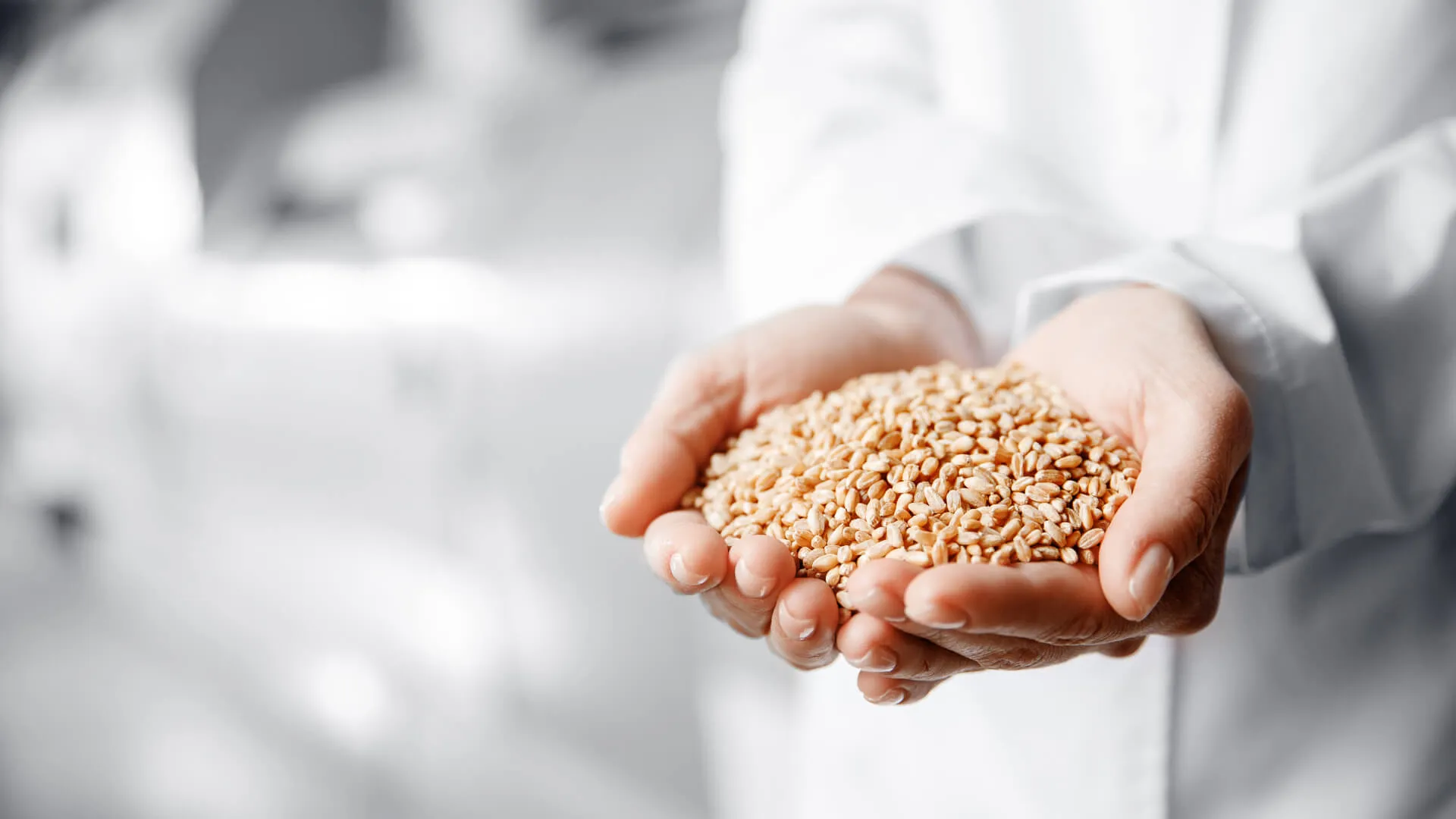
In this article, Jon Gilchrist, KPM's Technical Solutions Director for Vision Products, discusses why companies are choosing to use AI-powered vision inspection systems on meat and poultry processing lines.
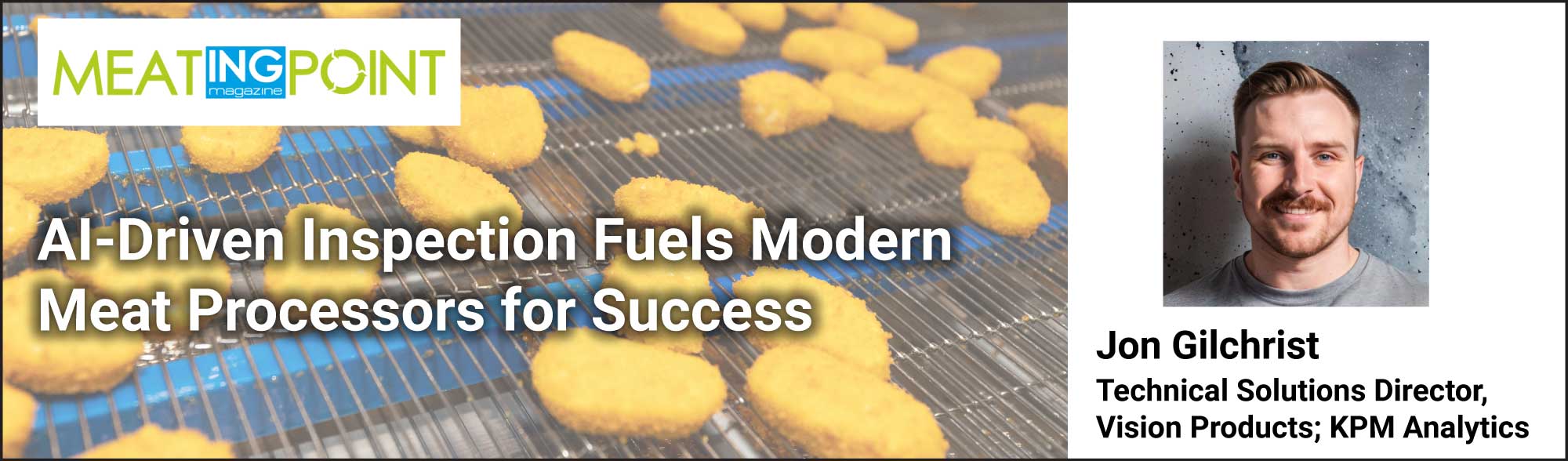
This article originally appeared in MEATing Point magazine. Click here to access the article on the publication's website (article appears on Page 18).
Quality control and food safety have never been more critical or challenging for meat and poultry processors and packers. Companies are being pushed to their operational limits to respond to increasing throughput demands, even though labor retention remains an issue throughout the industry.
Naturally, when a quality assurance team struggles to meet these demands, operations must slow down. There is also a higher chance of inspection mistakes, excessive or possibly unnecessary waste, or harmful foreign materials finding their way into the production stream.
These are only some reasons why many processing companies invest in artificial intelligence (AI) vision inspection technologies to meet these increasing demands and amplify their food safety efforts. New applications to streamline product grading and foreign material detection are emerging daily, making this an exciting time for companies to modernize their operations and gain a competitive edge.
An Evolution in Inspection Technologies
The landscape of available technologies to improve inspection and foreign material detection efforts has changed dramatically over recent years. Meat and poultry processing companies have used over-line X-ray and metal detector systems as vital quality control instruments for decades.
However, their primary use is detecting dense objects like metal, stones, and similar materials. They are less suited for soft foreign materials like paper, plastic, and films, which can damage processing equipment or lead to costly recalls.
Traditional technologies have limitations and lack accurate process insights, so automated, rule-based vision inspection systems have become popular a choice to meet the quality assurance needs of meat and poultry plants. Vision inspection technologies are sanitarily designed, incorporating high-resolution cameras, advanced lighting, and robust analysis software to measure various product features, whether used at-line, installed over-line, or integrated directly into a conveyor system. System measurements include anything related to the 2D size and shape of the product, 3D thickness, color, and marbling, but also more advanced measurements like blood spot or striation detection on raw products, bun coverage for processed products, trimming accuracy, predictive product weight, and more.
Vision inspection systems offer real-time analysis during production. When the system detects a defect or contaminant, it can alert the operator or automatically stop the production line. For some products, companies can integrate an automated rejection method to remove the out-of-spec products to keep the process moving. The immediate alert or action enables a safe and consistent quality control process, ensuring defective products or unwanted foreign materials never make it too far down the processing line.
Vision inspection systems today can be equipped with hyperspectral imaging technology for advanced foreign material detection and classification. Hyperspectral imaging uses a combination of spectroscopy and imaging technologies to acquire images of products at non-visible wavelengths, amplifying the system’s capability to find potentially harmful foreign materials on the product’s surface.
Even more recently, vision inspection systems have been deployed with advanced AI-driven machine learning capabilities to increase ease of use, achieve higher detailed measurements, and detect foreign materials with remarkable accuracy. The automated learning of product features and specifications dramatically reduces system complexity and promotes continuous operations to keep systems running longer with less human intervention. An AI vision inspection system never takes a vacation or a sick day. It can deliver the same precision and accuracy if it remains in operation or until trained for a different production line or SKU. Facilities can integrate their collected data into factory control software to create a feedback loop if desired.
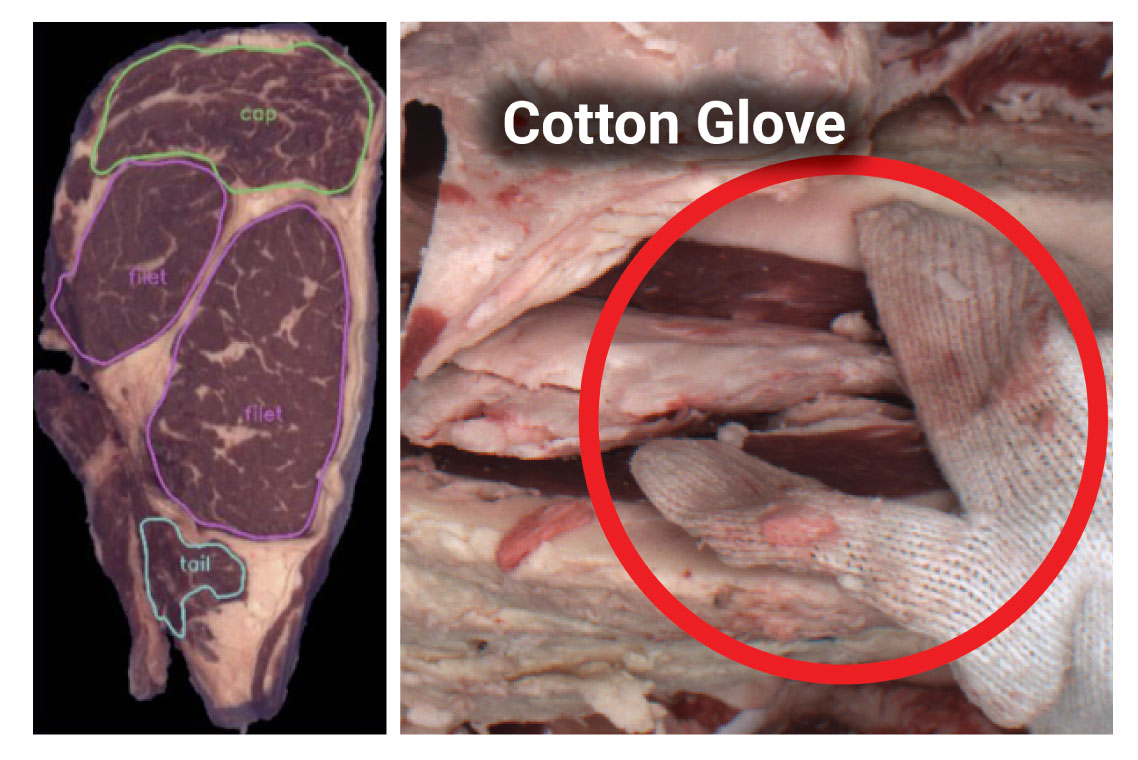
Right: Glove identified in a beef trim line by artificial intelligence.
Nevertheless, with access to more inspection and process control data than ever before, many operations using advanced vision inspection systems may not realize the full capabilities of their vision technology investment.
Optimizing Production Processes by Leveraging Inspection Data
Automated AI-driven vision inspection technologies allow companies to analyze 100% of products when integrated into their processes. This valuable data helps support the efforts of various groups within an organization.
Production Line Level Impacts
As its original use, an integrated AI vision system enables operators on the processing floor to make better-informed food quality and safety decisions. For example, a chicken nugget company producing 3 million chicken nuggets per day will see some percentage of waste. Relying solely on manual inspection of products for their overall size, shape, breading color and coverage, or other product features is a challenging task at full production speeds. Additionally, at the time a quality issue is discovered (e.g., the breading color becoming too dark because the fryer oil needs changing), several products have already been wasted.
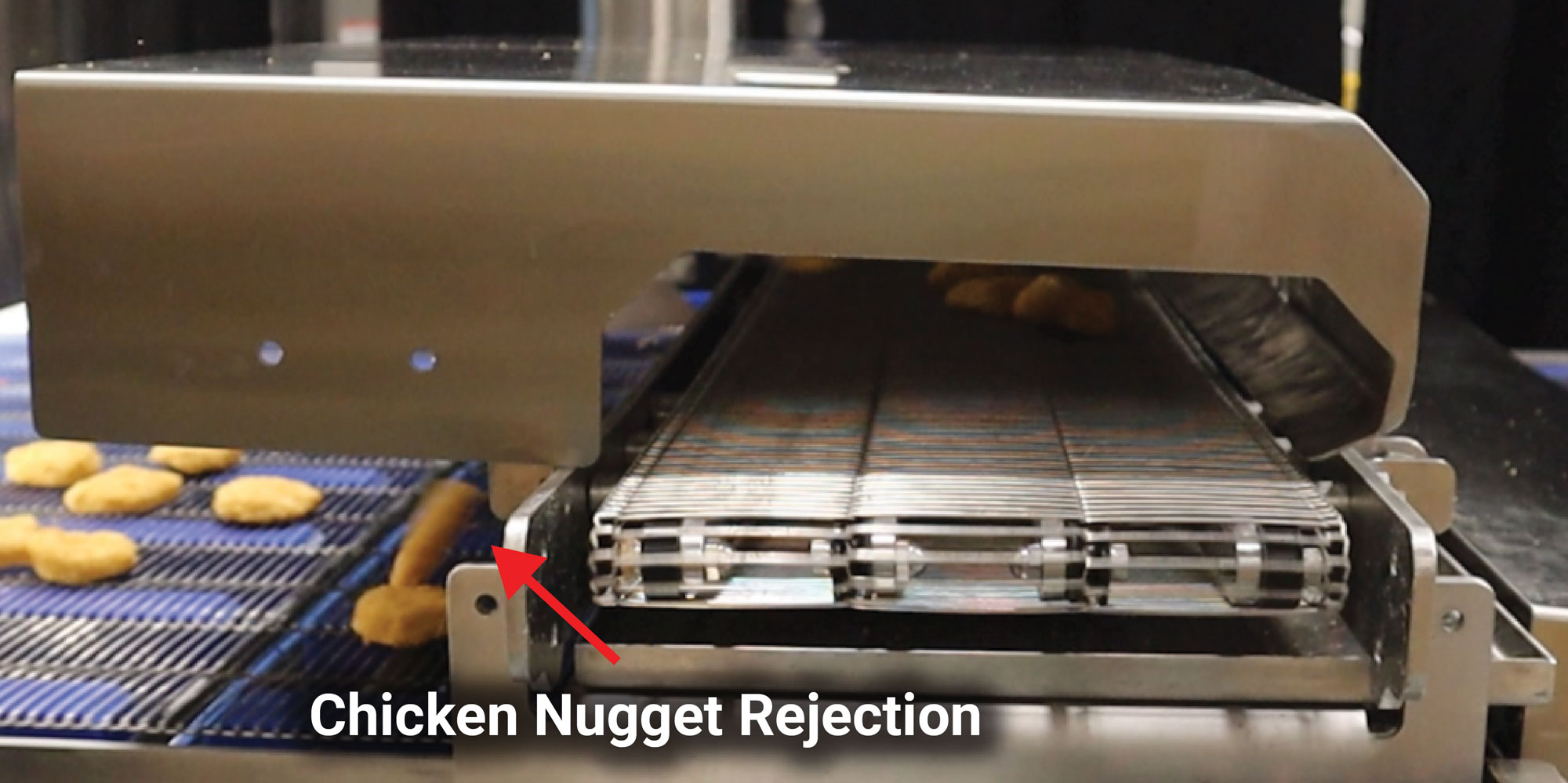
Because in-line inspection systems can interface with existing MES and SCADA systems, they can help detect when products may start drifting towards becoming too dark after exiting the fryer and take immediate corrective action or alert the operator.
For that 3-million-a-day chicken nugget producer, lowering their waste by as little as 0.5% (~150,000 nuggets at 1 cent per nugget) equates to significant savings over time because the operator can make better-informed decisions on process control thanks to their vision data. Many companies have paid for their vision inspection systems quickly through waste savings alone.
Plant Level Impacts
There are multiple ways AI vision inspection can influence the accuracy and decision-making of plant-level processes. First, the technology helps determine the root causes of common process issues.
Take a hamburger patty manufacturing company, for example; all patties must be formed to a specific size or shape to ensure they are cooked thoroughly and fit correctly within the product packaging. If a plant has multiple forming machines feeding products to later production stages, having an integrated vision inspection system that continually measures the products exiting the formers helps detect any issues like double-stacked patties, edge defects, excessive patty cupping, worn forming equipment, and much more.
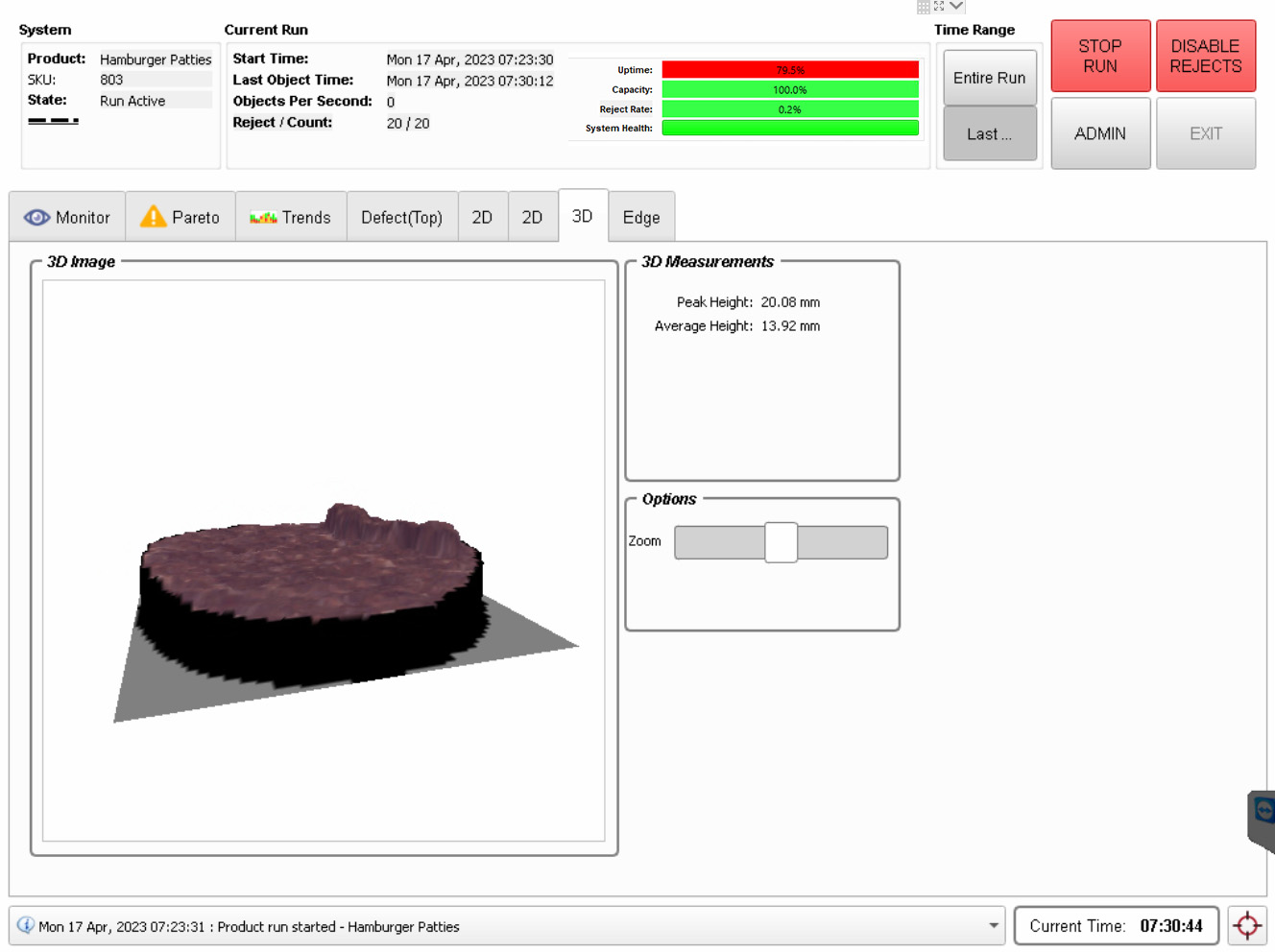
Using this data, the company can clearly identify the forming machines that routinely have product consistency issues. If all process adjustments continue to fail, the plant manager can make a data-driven decision to have the equipment serviced or replaced to prevent further waste.
Ingredient supplier evaluation is another helpful application. Companies change ingredient suppliers for various reasons, so an objective method to test new ingredients in the production process is a cost-effective way to safeguard supplier selection.
Going back to the chicken nugget producer, let's say the company is switching breading suppliers and has received samples from multiple suppliers to test their production process. Whether testing individual products on an at-line system or using an over-line system positioned above a product stream, the plant managers can quickly assess whether the breading cooks correctly, adheres to the product throughout the process, maintains texture, and other visual attributes. Being able to compare product appearance against programmed values, rather than relying on color charts or operator interpretation, is an effective way to help ensure a seamless transition to a new ingredient supplier.
Corporate Level Impacts
For large meat and poultry processing companies, AI vision inspection technologies go a long way in helping analyze performance trends across multiple locations. Some vision inspection systems offer software modules that allow users to generate plant-wide performance reports on anything from product rejection rate to the color or presence of visual attributes on a product.
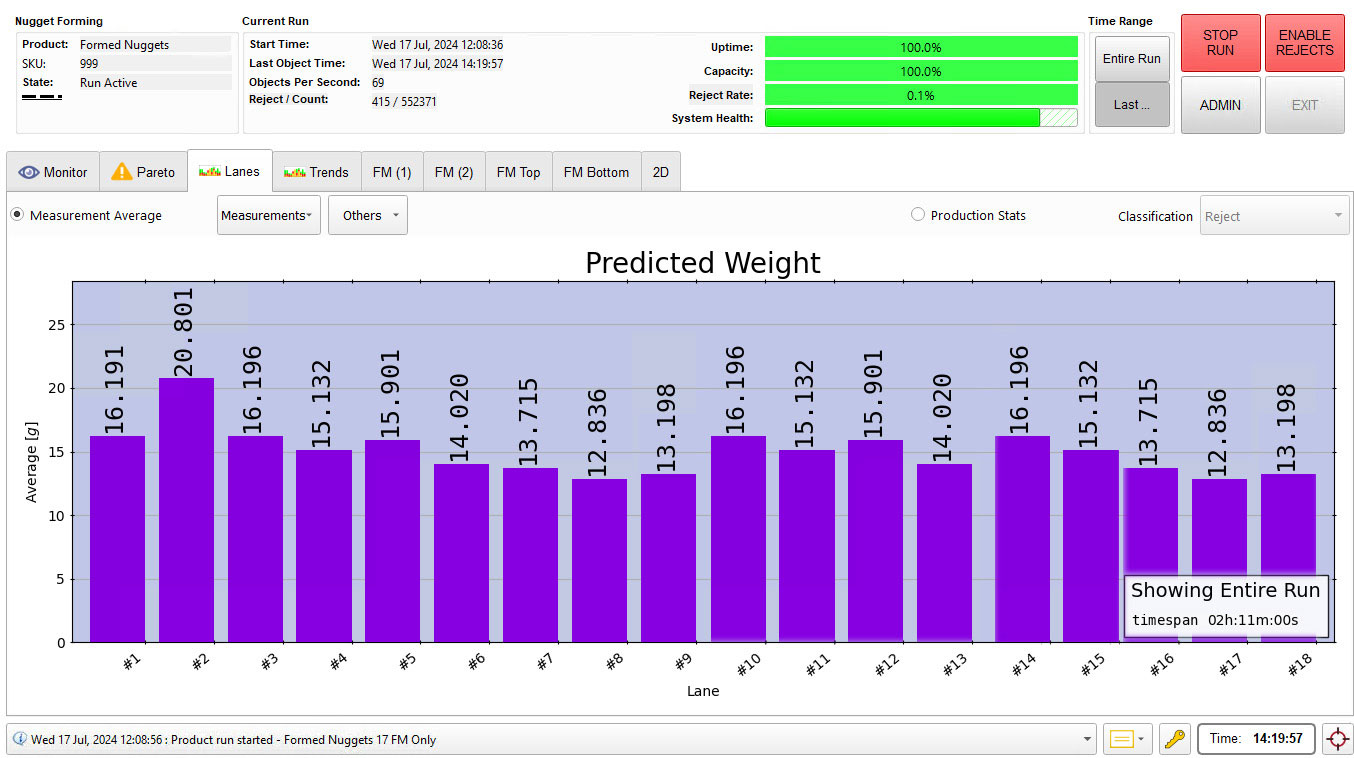
Having access to this data not only helps companies deploy higher standards for product consistency company-wide but also aids in the decision to invest capital resources to correct global challenges. This benefit is especially useful for companies with multiple production sites; if vision systems are on all production lines, benchmarking performance company-wide and addressing potential production issues becomes much easier.
Regulatory compliance and traceability are essential for meat and poultry processing companies. Vision inspection technologies provide data that prove quality and safety measures are maintained throughout the organization. These technologies can help companies deliver on their promise of top-quality and safe food products. Every avoided recall due to an inattentive inspector will help companies protect their bottom line and avoid the public relations troubles that follow.
Improved Decision Making Throughout the Organization Made Possible with Robust Inspection Data
Product consistency is a significant factor in a customer’s brand loyalty. The more companies can do to align quality assurance efforts across their many locations, the better positioned they will be to meet the needs of increasingly demanding global scale customers.
Data from AI vision inspection technologies help quantify product quality, process performance, adherence to regulatory requirements, and the success of their food safety efforts. The more ways companies can utilize this valuable inspection data in their operations, the better prepared they will be to address growing demands and stand out from the competition.
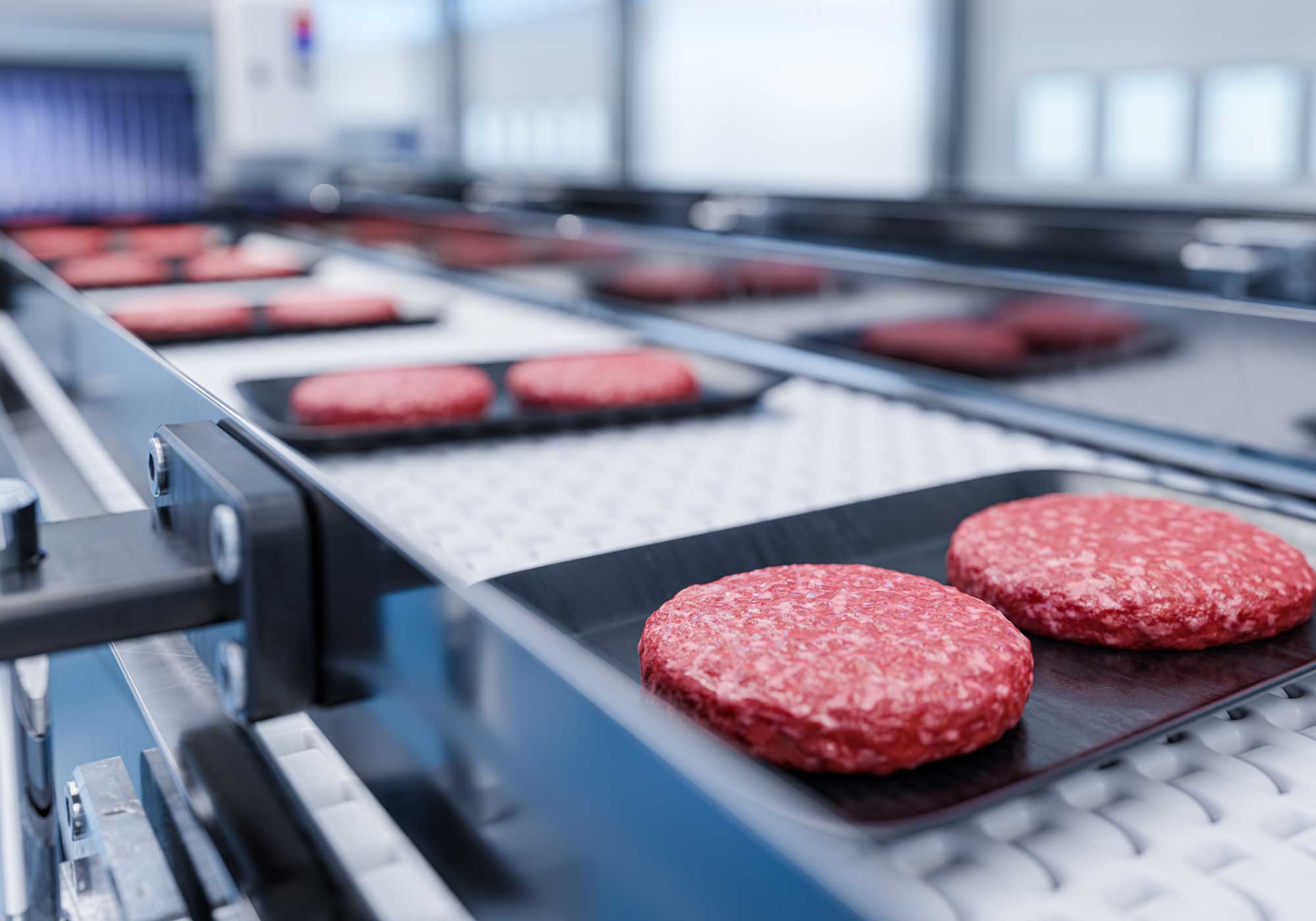