AI Provides a Dependable “Eye” for Challenging Foreign Material Detection
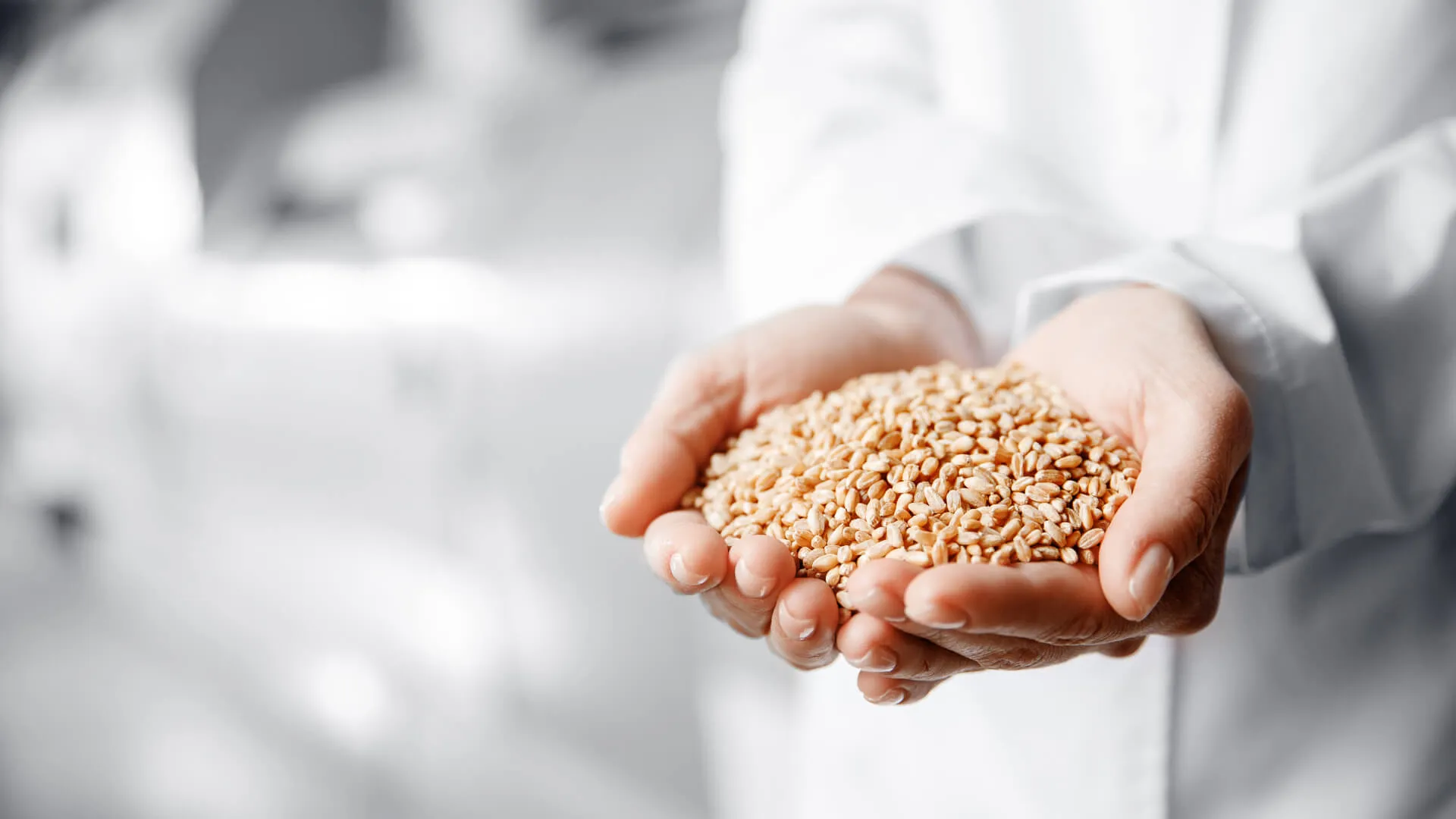
In this article, Jon Gilchrist, KPM's Technical Solutions Director for Vision Products, discusses how AI-powered vision inspection systems can help companies detect foreign materials and avoid costly recalls.
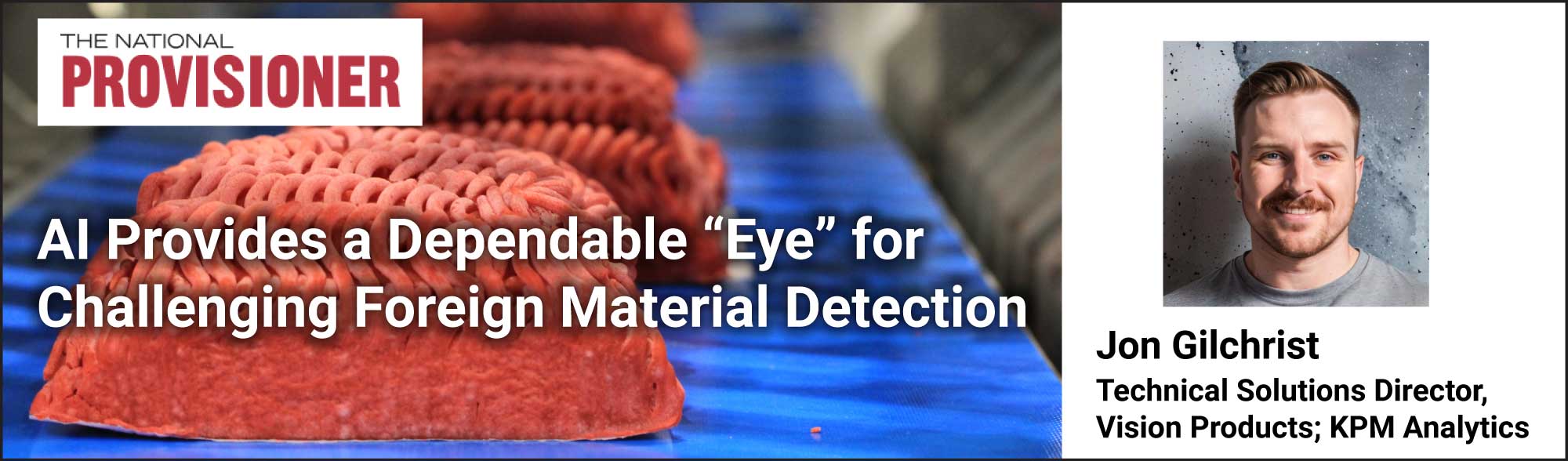
This article originally appeared in National Provisioner Magazine. Click here to access the article on the publication's website.
For many reasons, meat processing companies have always had the challenge of retaining and training online product inspectors at their plants, despite the fact they are vitally essential to a company’s quality and food safety programs. Nevertheless, all it takes is one product recall due to inaccurate detection of unwanted or harmful foreign materials on food products to cripple a company financially and its brand’s perception in the market.
The average cost of a product recall can vary widely depending on the industry, the scale of the recall, and the specific circumstances involved. In the food industry, for example, a study by the Food Marketing Institute and the Grocery Manufacturers Association (now known as the Consumer Brands Association) has estimated that the direct costs of a recall can average anywhere from $10 million to $30 million. This estimate includes expenses related to notifying consumers and retailers, pulling the product from shelves, destroying contaminated products, and managing public relations.
Therefore, meat processing companies that invest in automated technologies to protect their operations and customers from potentially unsafe food products can mitigate these risks effectively.
Traditional methods for foreign material detection have limits
When it comes to detecting dense and solid objects – metal tags, stones, broken pieces of machinery, etc. – X-ray and metal detection systems have been a reliable solution used by meat processing companies for decades. However, low-density or soft objects pose an equally damaging risk should they find their way into the process. X-ray and metal detectors are not well suited to detect materials like rubber, paper, plastic and films, wood chips, etc.
Computer/machine vision inspection technologies driven by artificial intelligence (AI) have quickly become popular among meat processing companies as a dependable option to detect these challenging foreign materials. These sanitary inspection technologies integrate within critical stages of a processing line to analyze products in real time and benchmark their product attributes against pre-programmed standards for product quality and appearance. Virtually anything that a human inspector can perceive can be programmed into a product measurement code, thereby creating objective, quantifiable measurements for what has previously been a subjective process.
Meat processors benefit from recent advancements in AI vision inspection
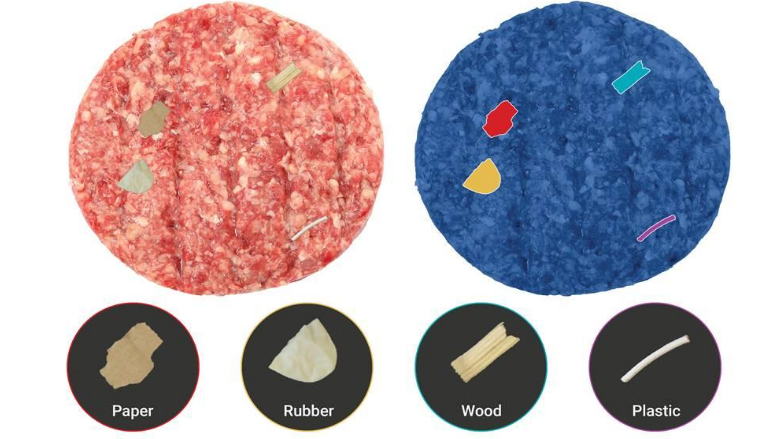
At the heart of an AI vision inspection system is its machine learning algorithms. Like a line worker, the algorithm requires training, using vast datasets of images labeled with information about desired quality, known defects, and other relevant characteristics that human spotters are trained to recognize.
AI vision inspection systems are trained to detect virtually any foreign material on the surface of a food product with high precision. Additionally, unlike rotating shifts of workers, once trained, the AI vision system can deliver the same precision and accuracy if it remains in operation or trained for a different production line or SKU.
Some AI vision inspection systems include infrared imaging to analyze non-visible materials like moisture and oil content. These attributes provide further insight into the composition of a product, adding a deeper layer of protection to inspect foreign objects that are similar in color to the final product, which most human inspectors can easily miss.
An aid to labor – not a replacement
AI vision inspection addresses an area of most meat processing organizations that has traditionally been difficult to manage: Labor retention at critical quality control positions within the organization. Nevertheless, with AI being a hotly discussed topic throughout our world today – especially regarding its impacts on worker responsibilities in a variety of industries – in the case of vision inspection technology, it can provide many positive productivity impacts for companies. Rather than having a full-time product inspector on the line or continually spending the time, effort, and money to train new employees on these tasks, companies can give that individual a more meaningful role elsewhere in the plant.
Meat and poultry companies can transform their quality assurance and food safety efforts by integrating AI vision inspection technology, especially when identifying traditionally difficult-to-detect foreign materials. As more companies invest in AI vision inspection technologies, the models and capabilities for these robust systems will expand, improve, and revolutionize quality control capabilities for meat and poultry processors.
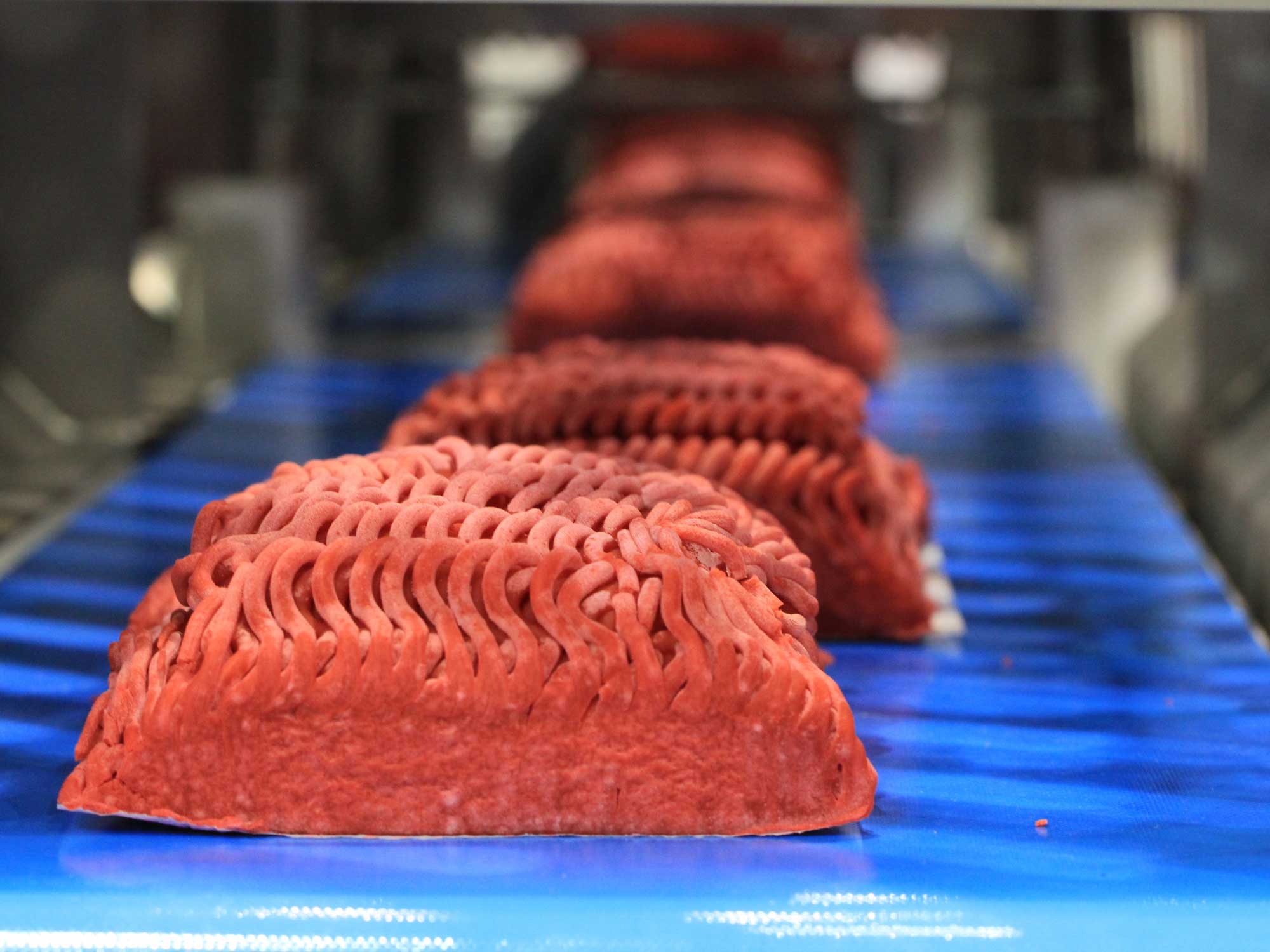