Careers
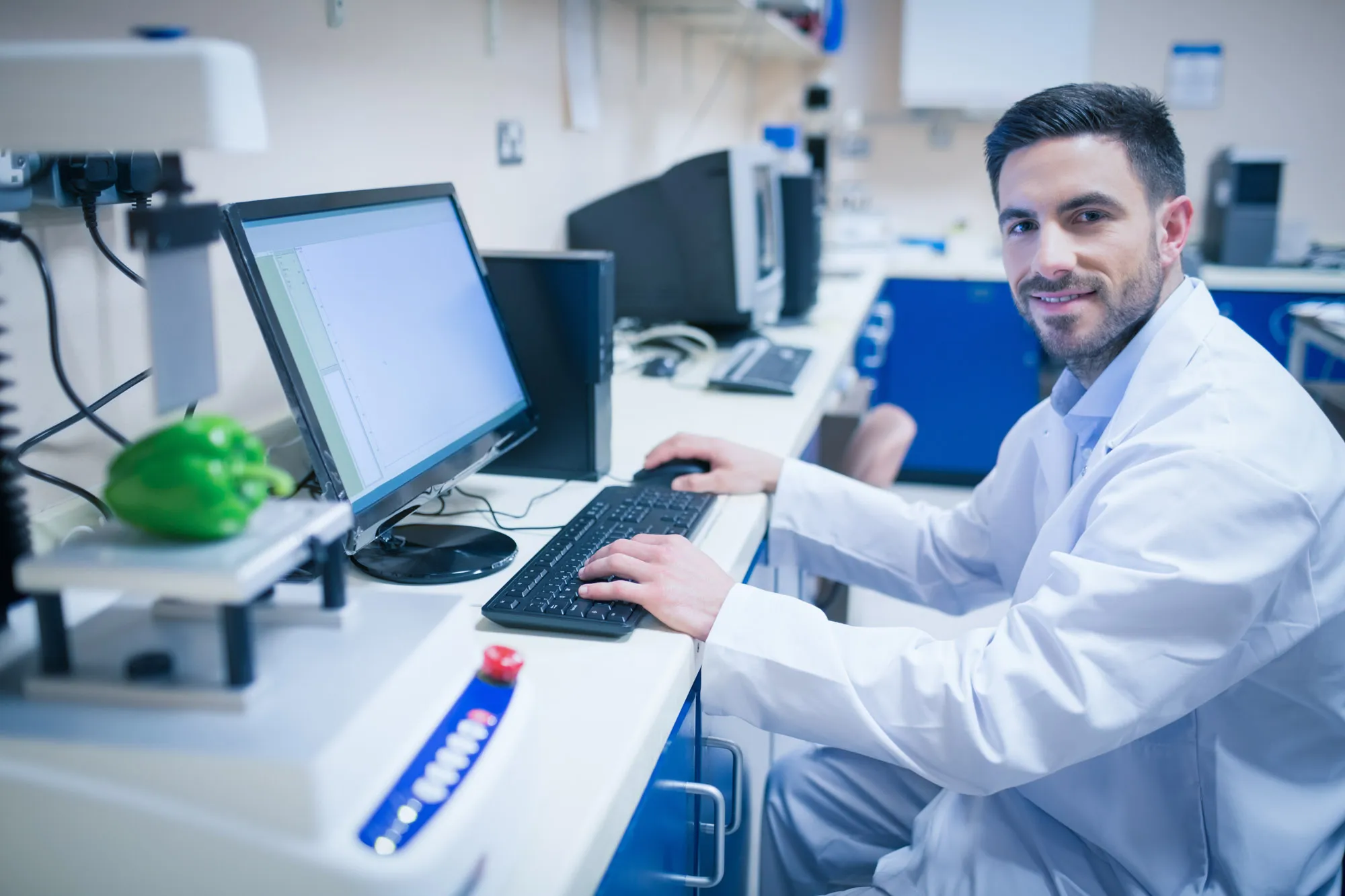
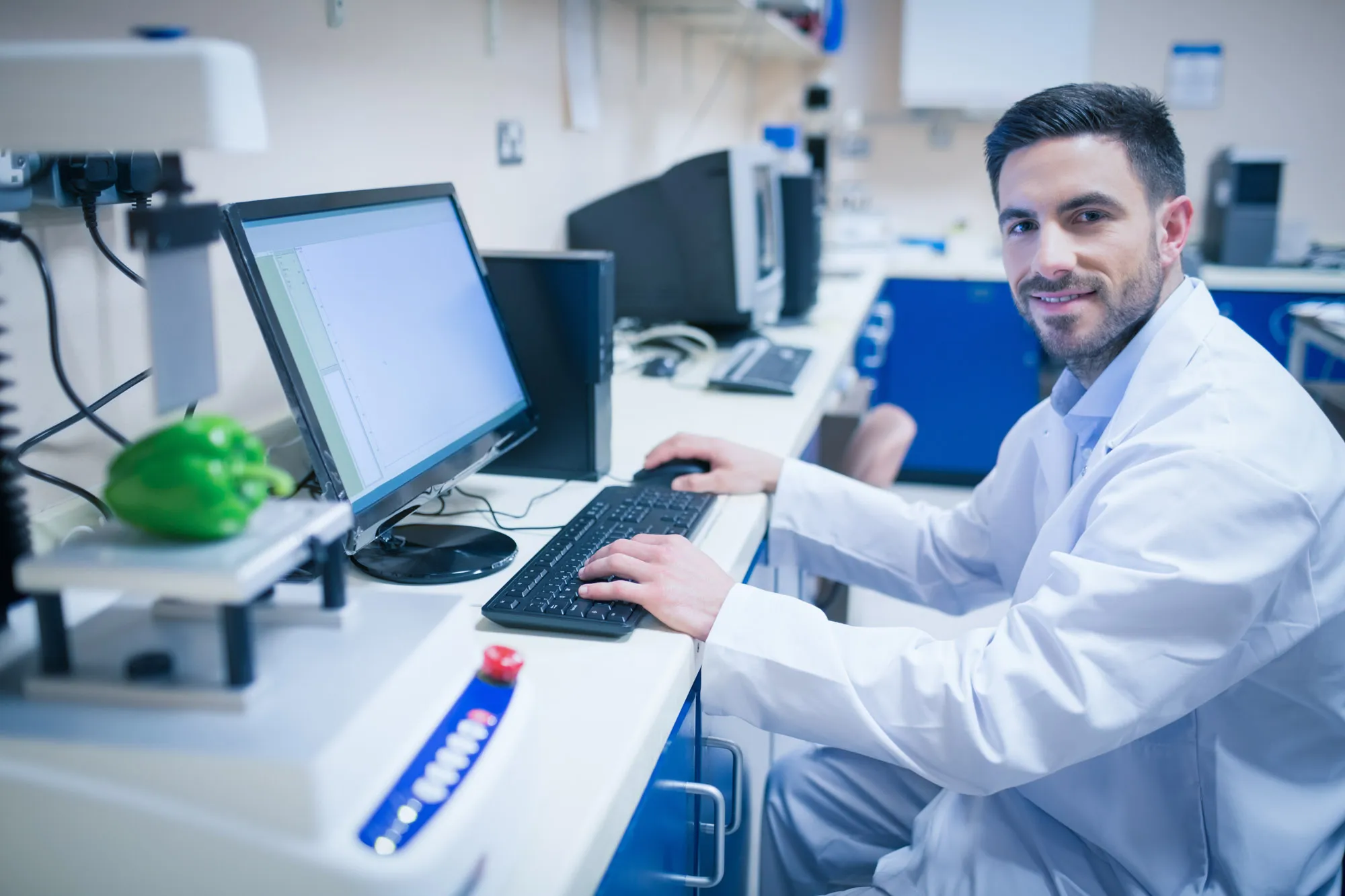
Are you a curious job seeker looking to help customers advance their automated systems and bring efficient technologies to their business? Check out our career opportunities and apply for one of our open positions.
Open Positions
At KPM, our most valuable resource is our people – with a diversity of backgrounds, ideas, and life experiences. We hire smart, creative, collaborative professionals who are always learning and sharing knowledge with the team. You bring the skills and a customer-first mentality, and we’ll bring the environment you need to be successful. Join our growing team today!
Thank you! Your submission has been received!
Oops! Something went wrong while submitting the form.
Unfortunately, we couldn't find any Open Postitions matching your criteria.
Reset Filters
This link leads to the machine-readable files that are made available in response to the federal Transparency in Coverage Rule and includes negotiated service rates and out-of-network allowed amounts between health plans and healthcare providers. The machine readable files are formatted to allow researchers, regulators, and application developers to more easily access and analyze data.
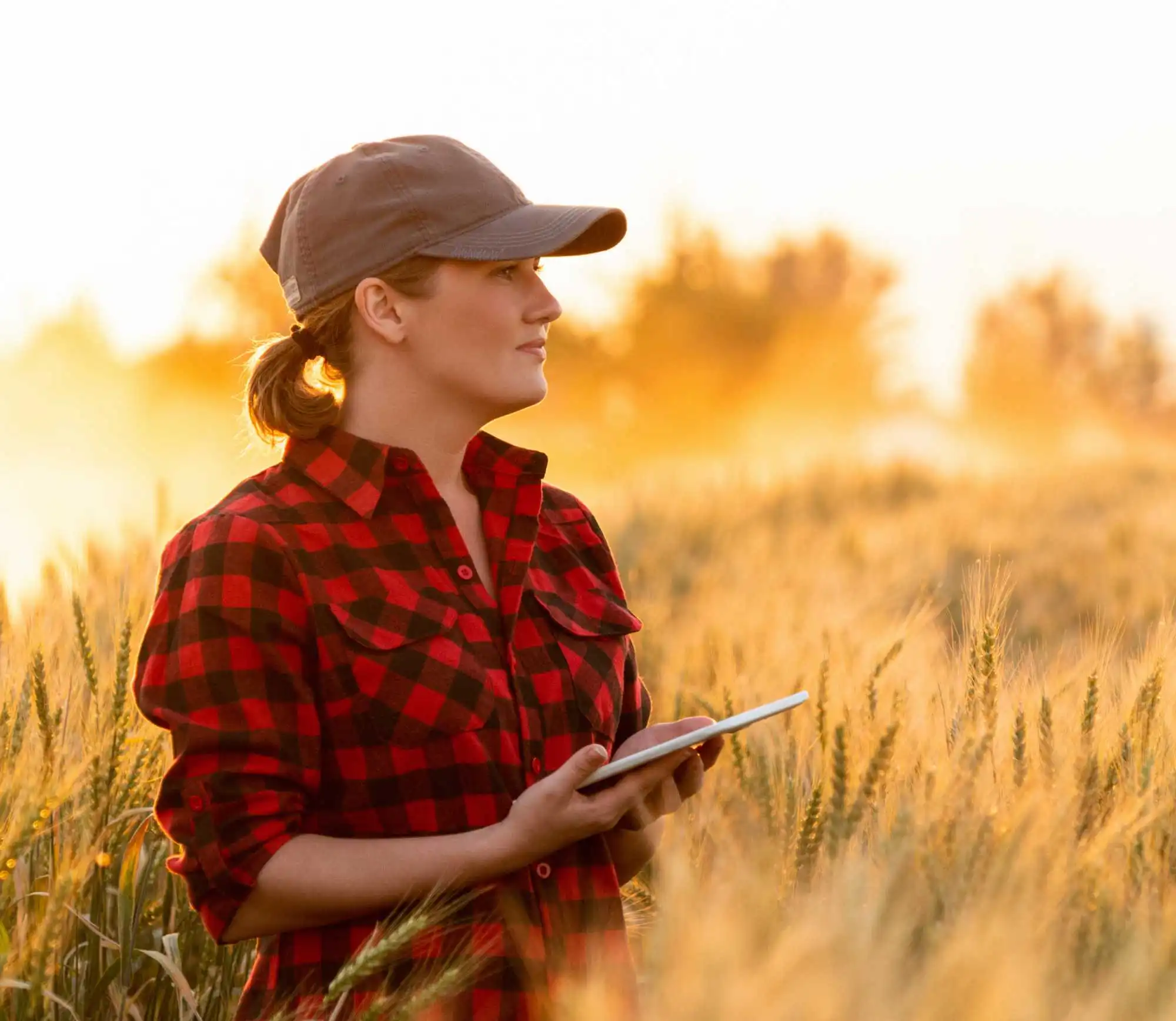
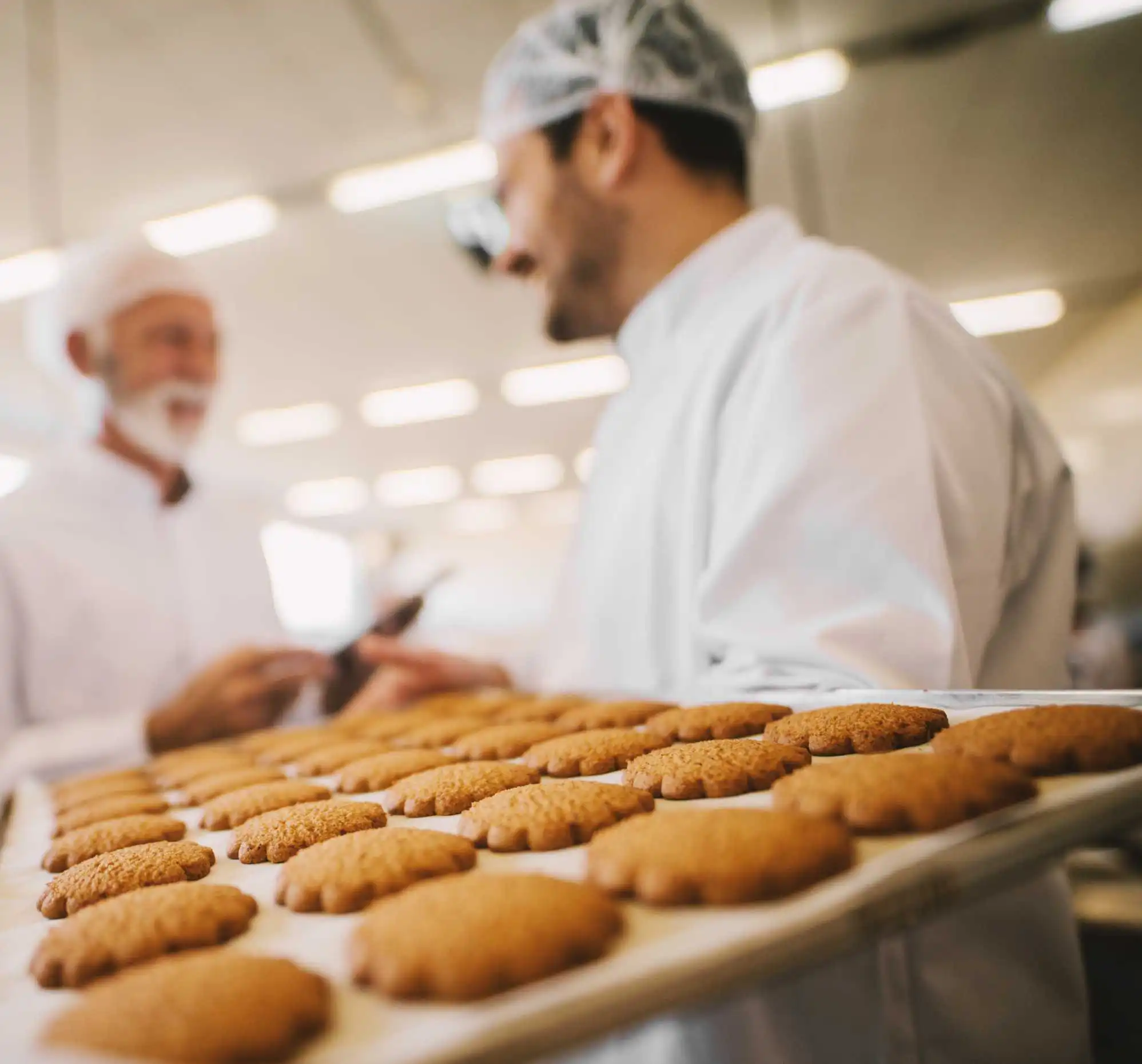
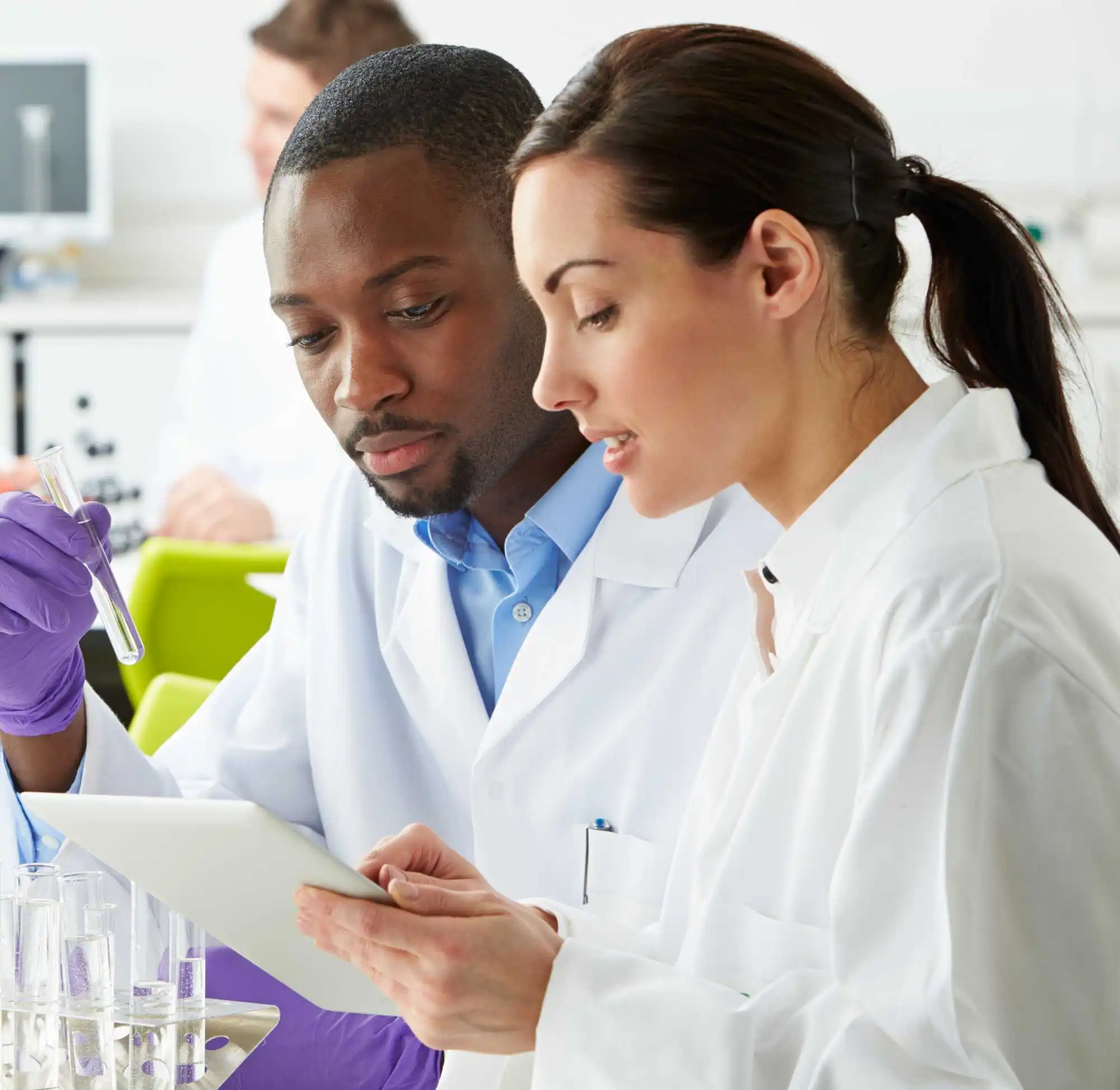
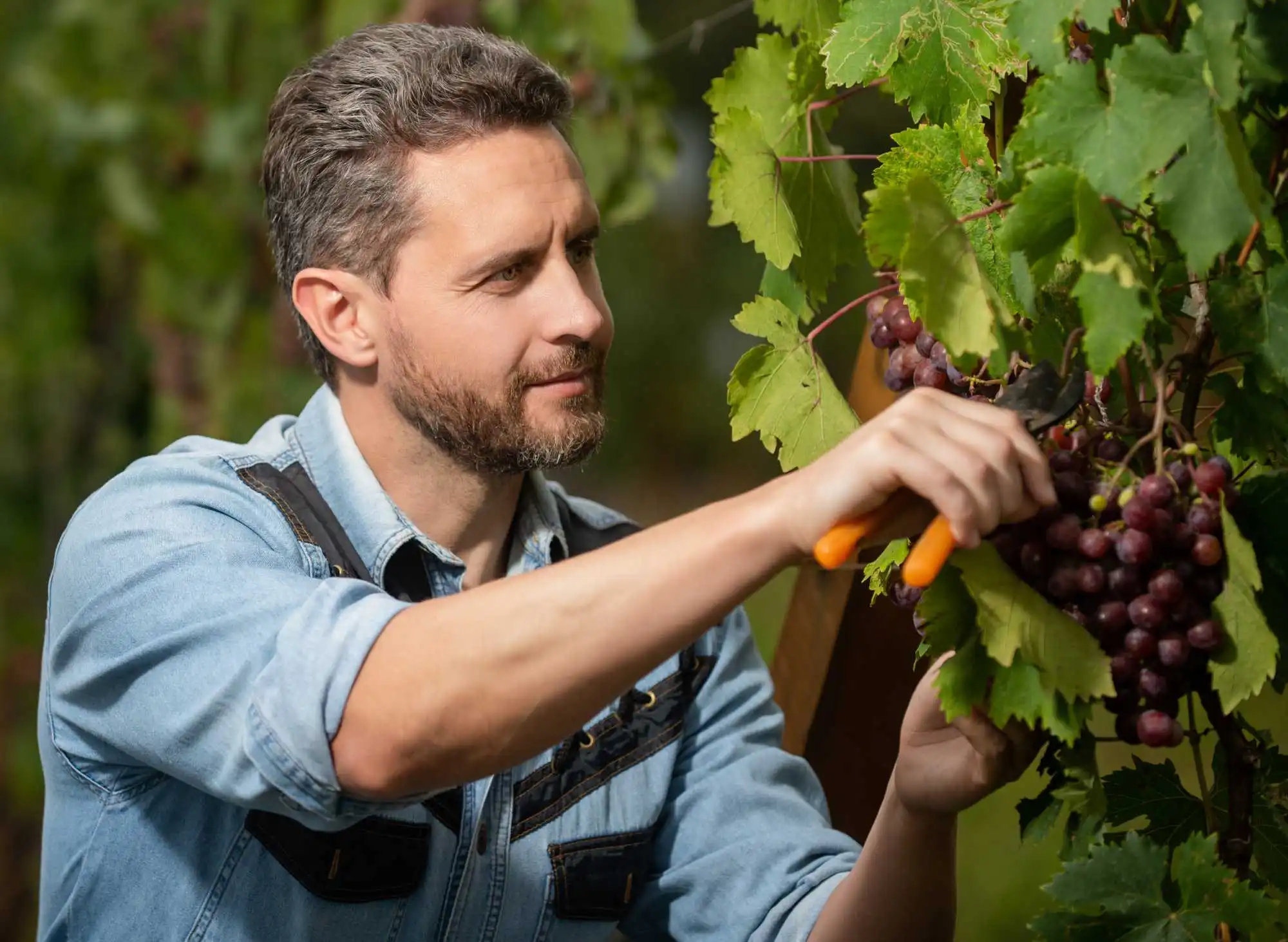