Tobacco Leaf Moisture Measurement and Control
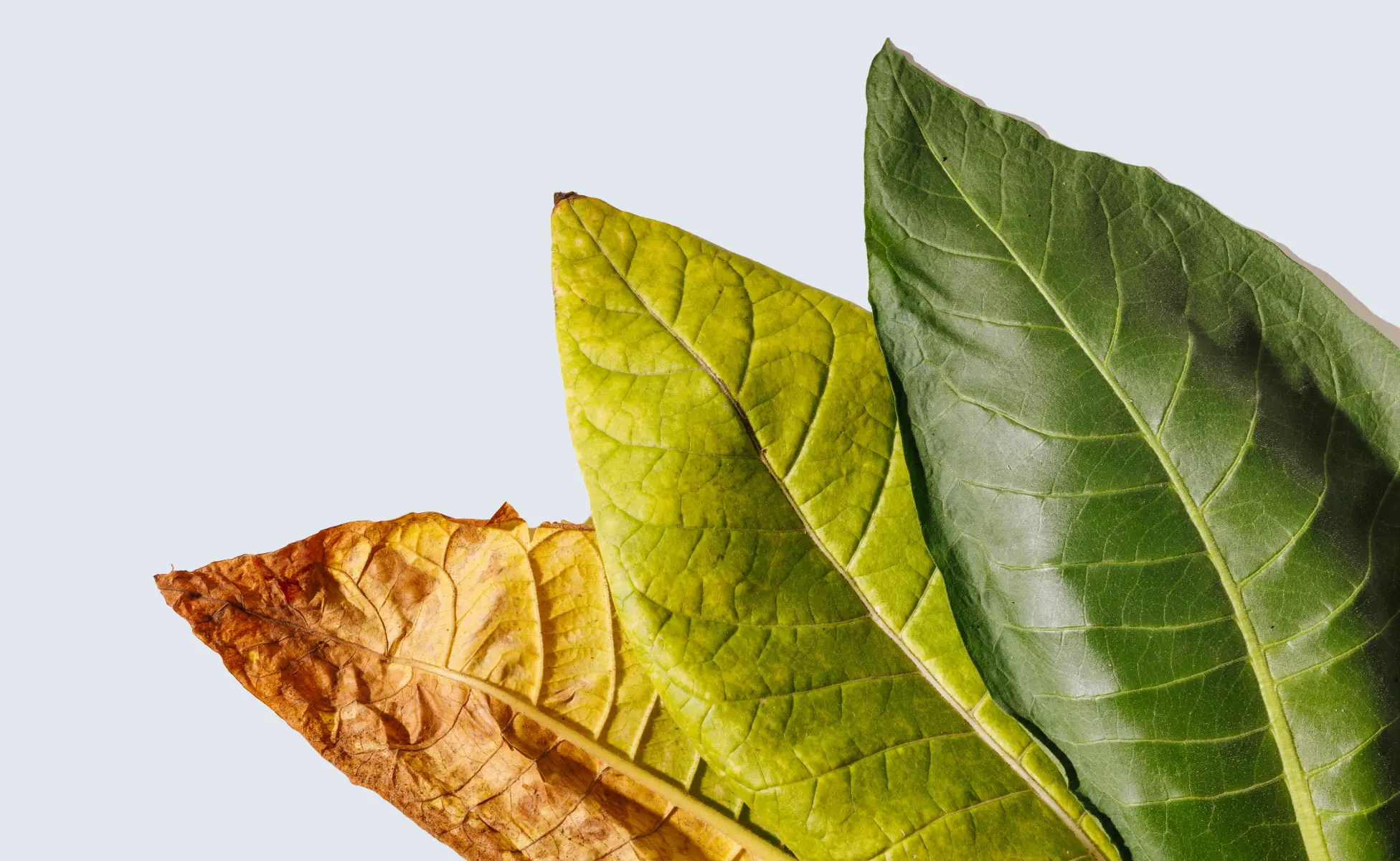
Table of Contents
Stages of Tobacco Leaf Processing
7.5 million of metric tons of tobacco are grown globally and are are used to produce 5.5 trillion cigarettes. As a highly valued crop, many steps are required to take tobacco leaves harvested from the fields and transform them into products such as cigarettes, cigar, pipe tobacco and other products. Tobacco leaf processing is the first stage.
Whole tobacco leaves contain a central stem (or midrib) and the leaf (lamina) which are mechanically separated at the leaf processing facility as they are used separately at the primary processing plant. Moisture content of these two parts is critical for the separation process (threshing) and when packing into storage cases in preparation for the production of finished tobacco products. Moisture impacts smoking quality, flavor, burn, fill, waste, and machine operation. Let's dive into the process.
Green Leaf and Stem Conditioning
To make the leaves ready for the mechanical threshing process, harvested tobacco leaves are conditioned in cylinders to be more pliable using forced hot air and steam. The conditioning cylinder is a rotating drum with independently-controlled steam jet nozzles that inject moisture into the tobacco. The conditioned tobacco then goes to the threshing process.
Tobacco Threshing Process
The conditioned leaf passes through a series of mechanical threshers and pneumatic separators. The thresher drums and blades tear the lamina from the stems, and the thresher produces a mixture of lamina, stems and un-threshed leaf. This mixture is fed into a classifier that separates the lamina from the un-threshed leaf and the stem. The lamina continues to the next process, while the un-threshed leaf and stems go into the next thresher. Threshing and classification is repeated until all the stem and lamina are separated.
The stem now moves on to the stem conditioning line, which gives the stem a higher moisture content than the green leaf. The stem is then processed through a stem cutter to give a consistent cut, and will then move to the drying process - similar to that of the lamina.
Drying
The lamina from the different classifiers has different moisture content, so the moisture has to be made uniform for proper storage of the lamina. The lamina first passes through a drying chamber to make the moisture uniform. The dried lamina is cooled and then passes into a high humidity conditioning chamber where the tobacco absorbs moisture and reaches equilibrium. The lamina is then packaged and placed into storage until being used. Stems are processed similarly on a dedicated drying line, to give a consistent product for storage.
Quality Parameters - Moisture
Green Leaf and Stem Conditioning
Efficient tobacco green leaf threshing (GLT) requires a conditioned leaf between 17 and 22% moisture content. To attain optimal moisture levels, green leaf tobacco is treated in conditioning cylinders with steam which can be adjusted to control the exit moisture. An accurate moisture measurement is critical to optimize GLT and achieve the desired strand length.
The stem is conditioned to around 40% moisture by controlling the steam levels to make it more pliable for the cutting process.
Drying
To safely store tobacco for extended times and to ensure a quality product requires a moisture level of the lamina and stems between 11 to 12%. When the lamina exits the drying chamber it is around 6 to 8%, and when it exits the humidity chamber it is at the final 11 to 12%. The final packed lamina and stems are typically stored for at least 6 months for aging or mellowing.
Measuring Points
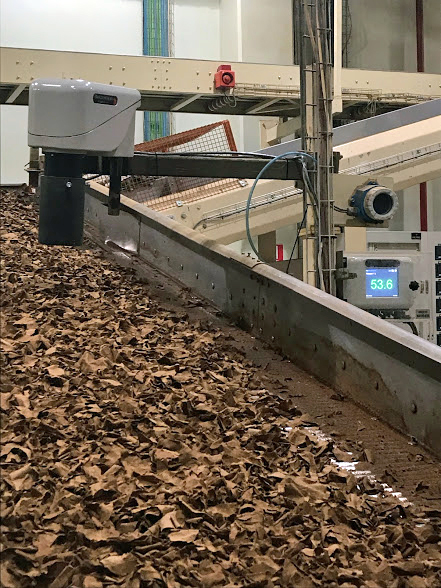
Green Leaf and Stem Conditioning and Drying
The MCT460 General Purpose Online NIR Sensor can be installed at the entrance or exit of the conditioning cylinder and the drying chamber, to provide real-time moisture readings. By using the standard 4-20mA/0-10v or optional digital output (ProfiNet, ProfiBus, Ethernet IP, Modbus TCP, DeviceNet) optimal efficiency of conditioning and drying can be achieved with closed loop process control.
The sensor is mounted 8 to 10 inches above and far enough down the conveyor where water vapor off the tobacco doesn’t interfere with measurement. An integrated IR temperature sensor can be added to the MCT460 to monitor tobacco temperature concurrently during the drying and conditioning processes.
Value and Quality
Throughout the tobacco leaf processing from green to finished lamina and stem, moisture control is critical. Having closed loop process control with a Process Sensors Corporation MCT460 moisture analyzer will provide optimal efficiency in all parts of the process. It will help to produce a consistent, high-quality end product that can be safely stored for months until being used for finished product at a secondary processing plant.
Related Blog Posts
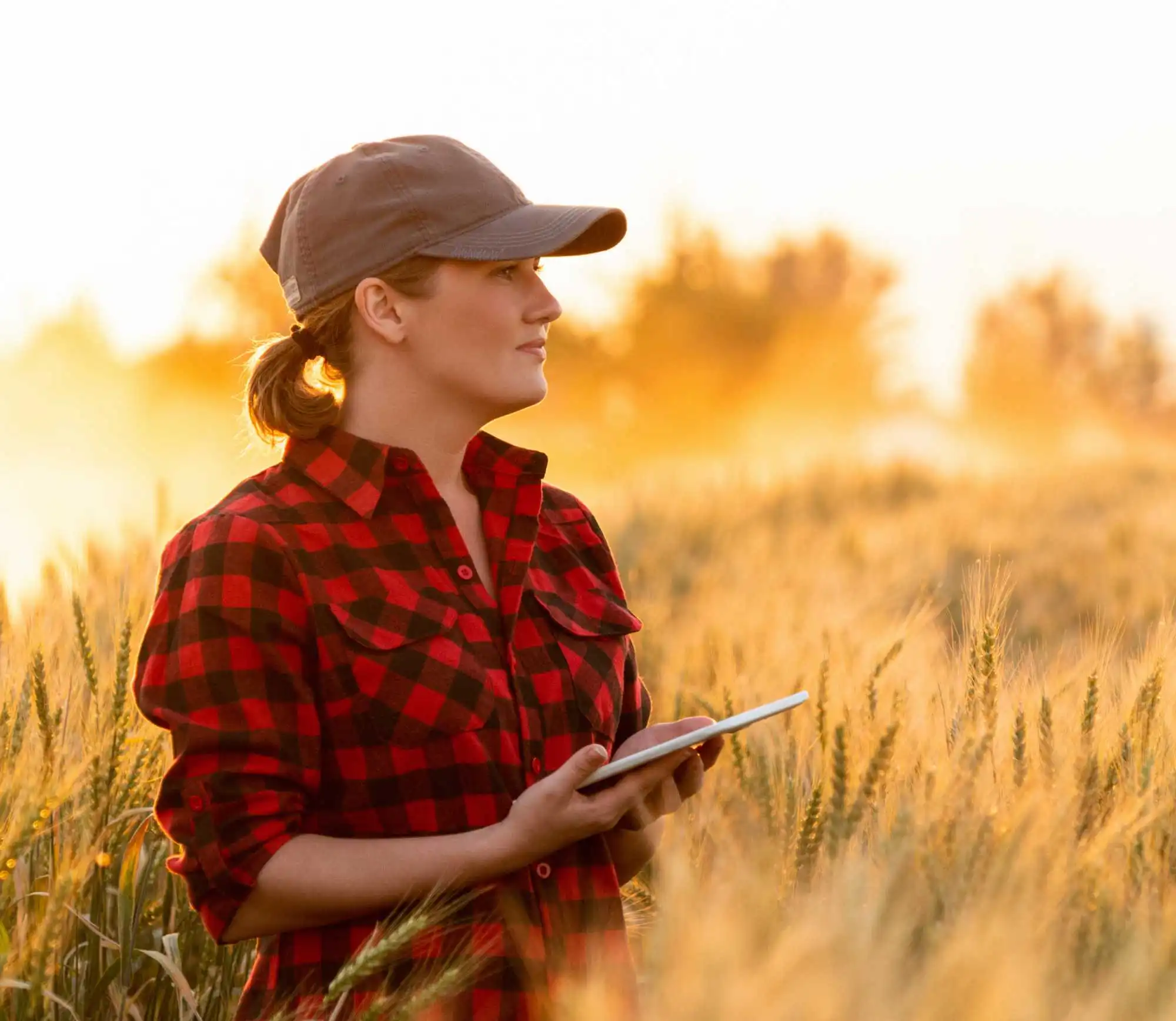
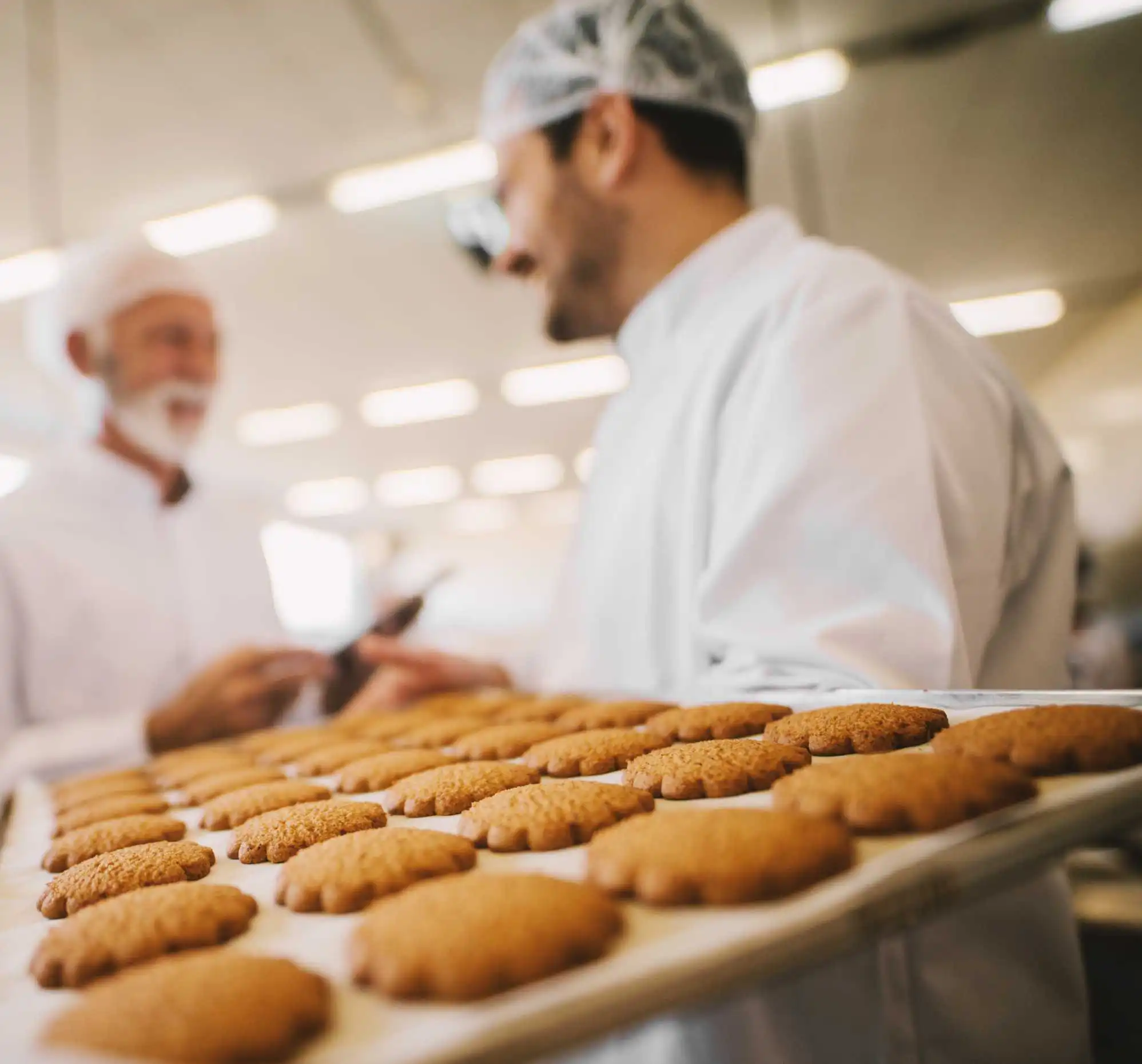
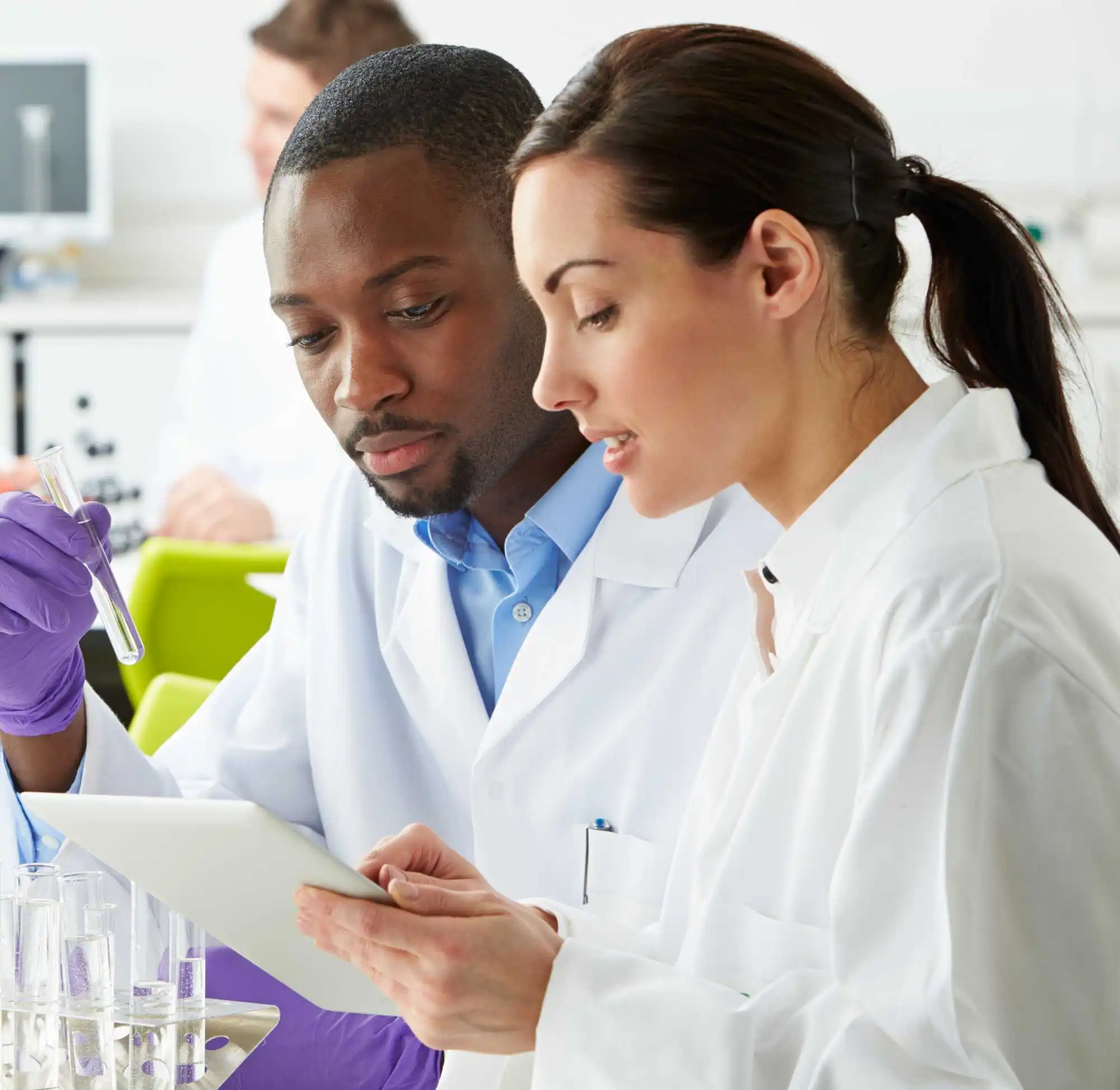
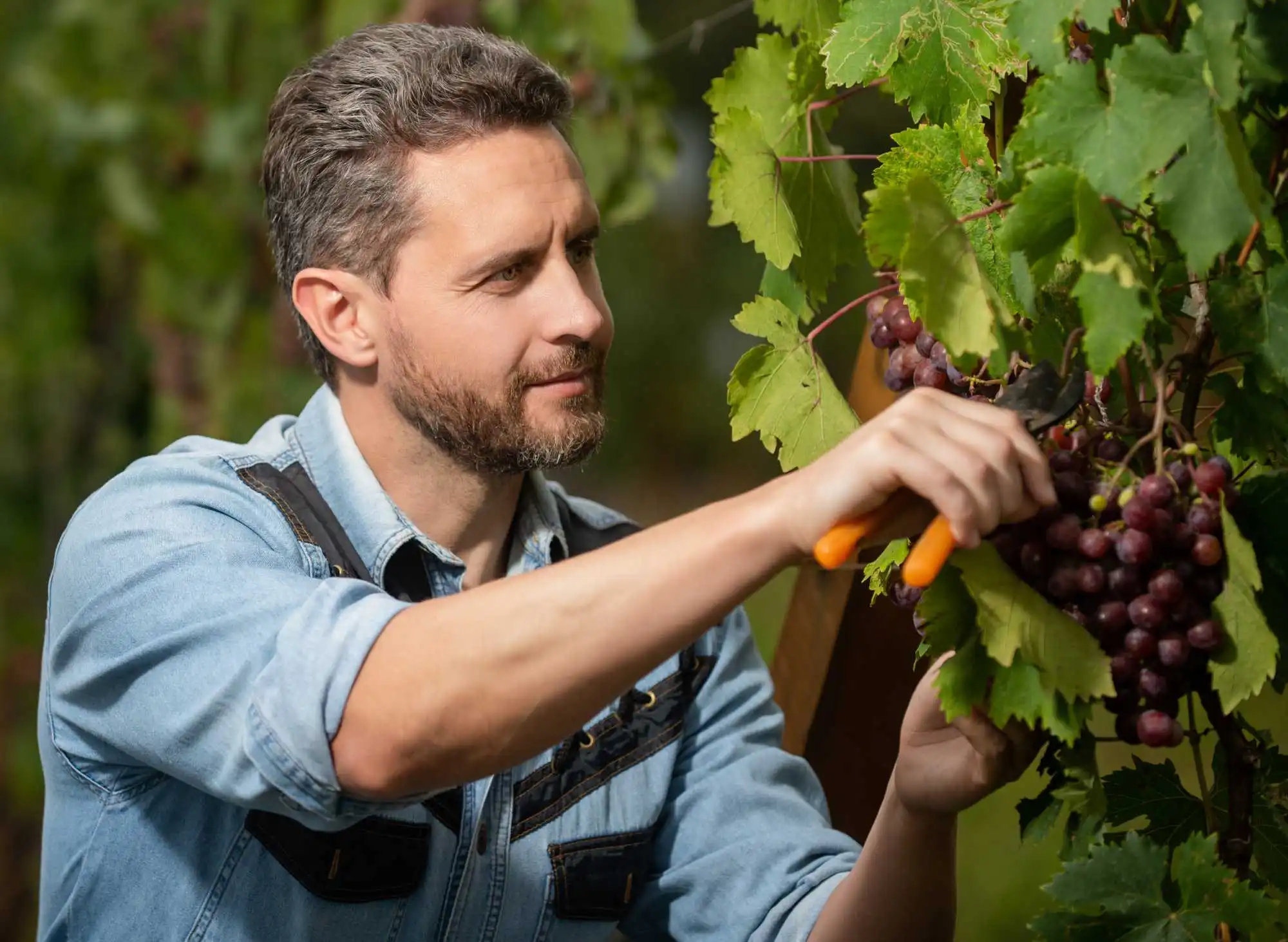