What is Vision Process Control
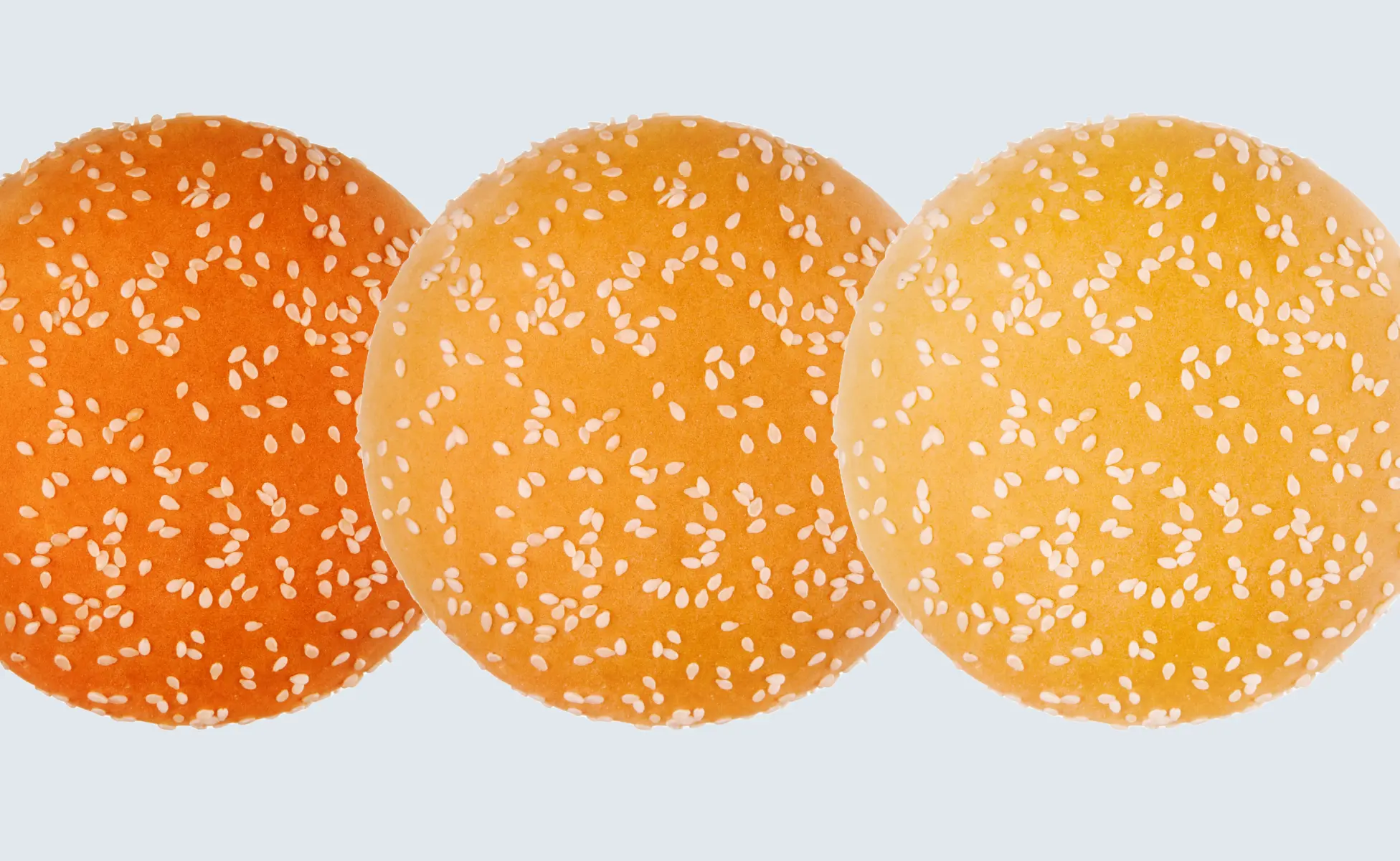
Table of Contents
Using Vision Inspection Data to Improve Your Process
When we think about vision inspection in food production, the first thing that many people think of is final product inspection. Most in-line vision technologies were indeed developed to verify visual traits like size, bake or fry color, presence of ingredients, and other cosmetic features.
However, several power users of vision technologies have been implementing more ways to utilize vision inspection technology to provide insights throughout their process. They have become the drivers of a new and growing category of vision systems called Vision Process Control (VPC) technologies.
Just as final product inspection technologies analyze the visual traits of final products to ensure they meet specifications before packaging, bakeries can apply these same principles to various stages of their unique production process.
Let’s take hamburger buns as an example; after the flour and ingredients are mixed into a dough, they must proof before entering the oven. Even if all production processes are controlled, there are several reasons why a dough does not proof correctly from batch to batch. Anything from the temperature and humidity in the production facility to poor quality yeast, too much salt, and several other factors can affect proofing.
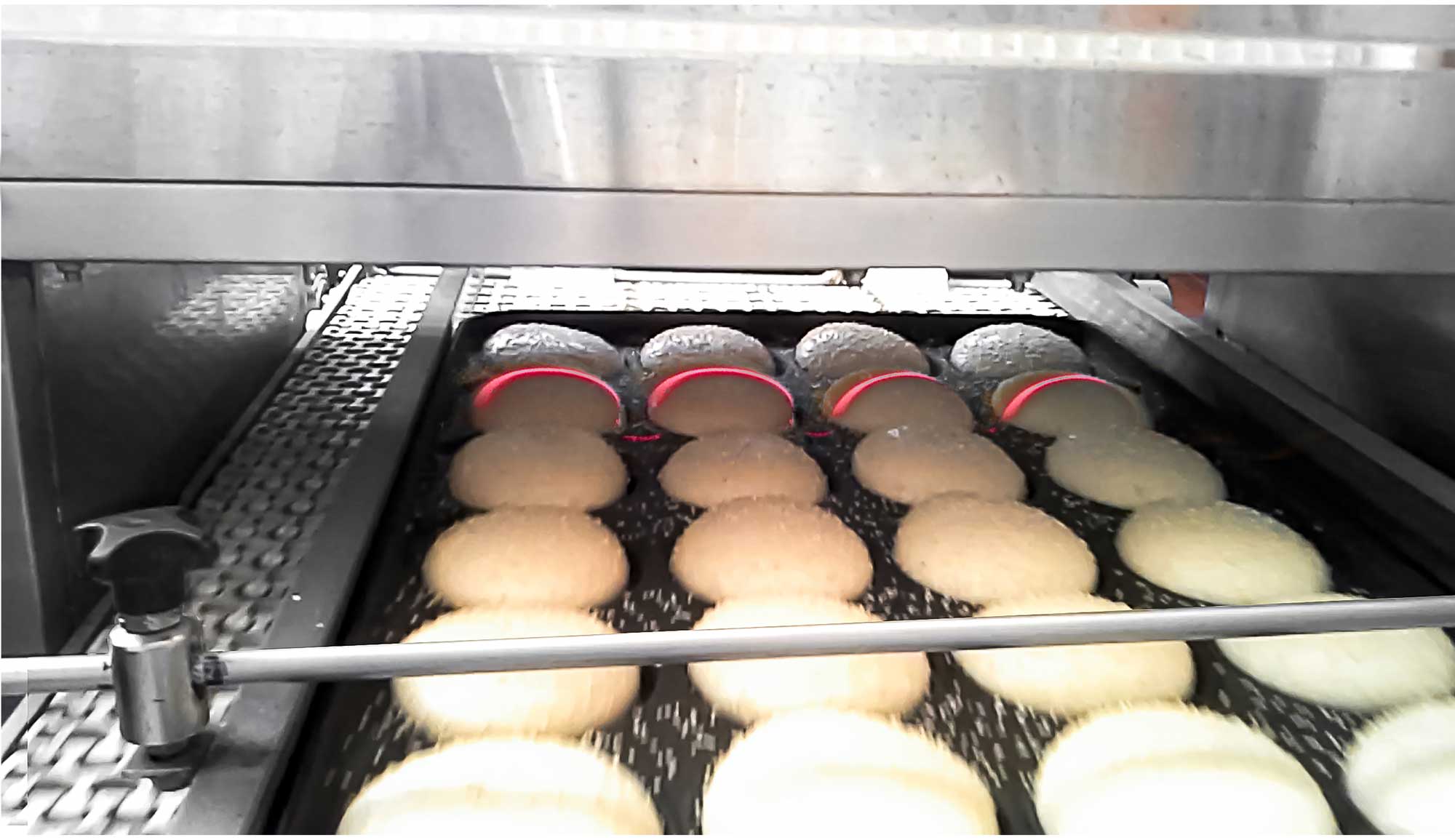
However, installing a VPC system to measure the 2D and 3D aspects of the dough before baking can detect the warning signs of a proofing process gone wrong. With access to this real-time data, operators can immediately address the production flaws.
Where Are the Common Trouble Spots in Your Process?
Due to space or safety constraints, it may be impractical (or impossible) to have a human inspector observe specific areas of the production process for trends that could signal trouble. With a VPC system, 100% process inspection is significantly more manageable and traceable, helping companies save waste and errors and ultimately make better production decisions.
Could VPC technology help you improve a trouble spot in your production process? Contact us today.
Related Blog Posts
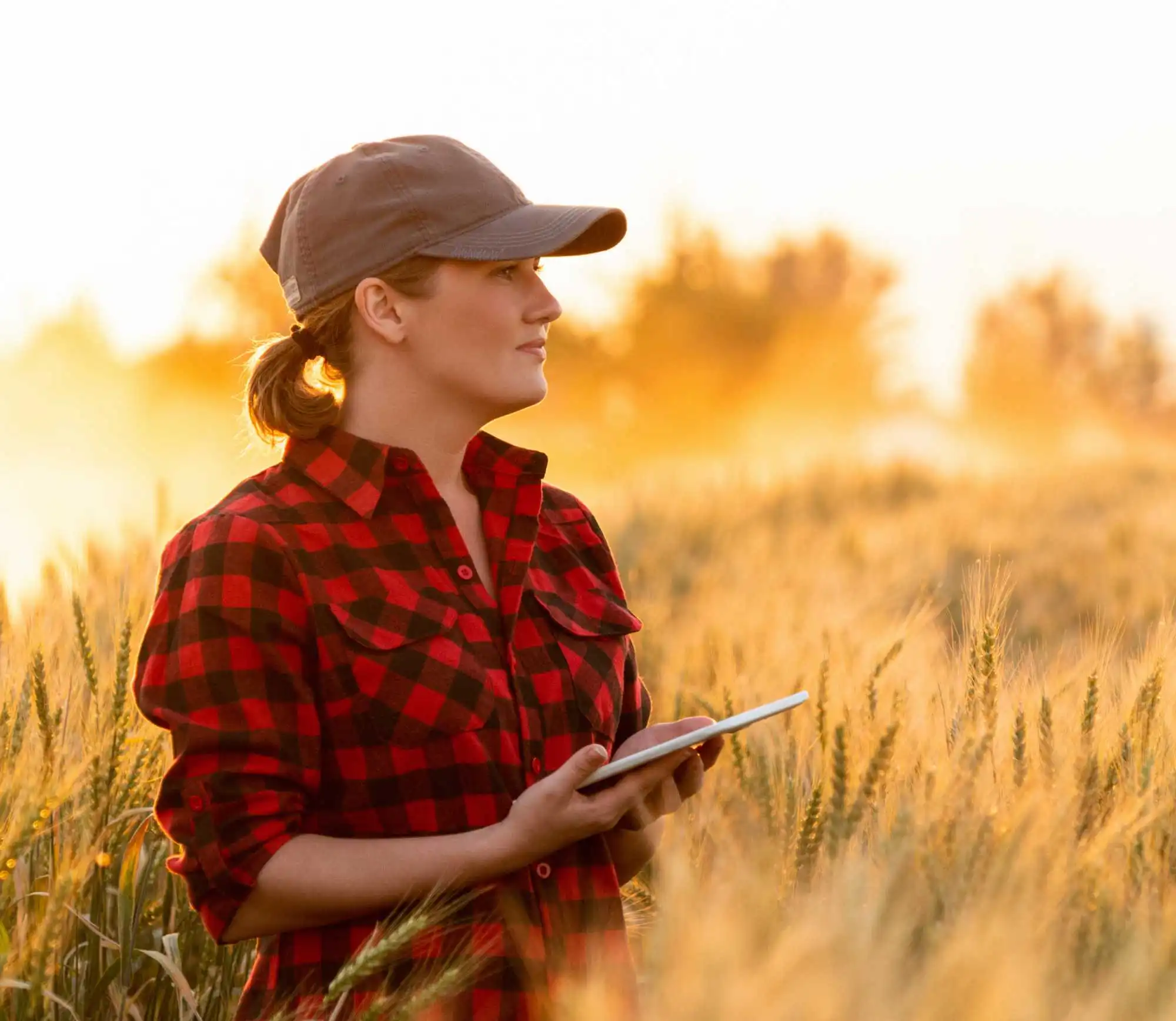
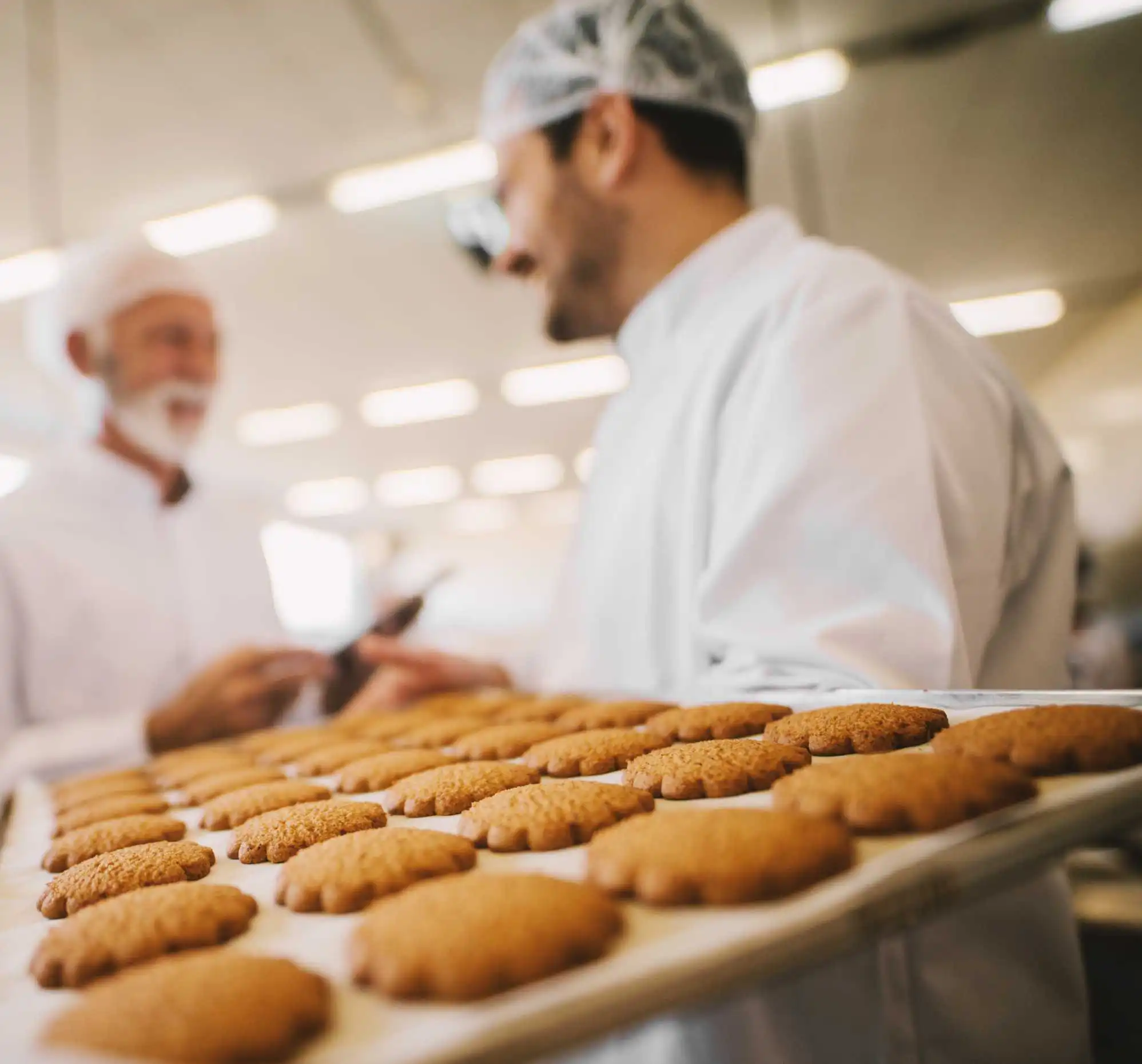
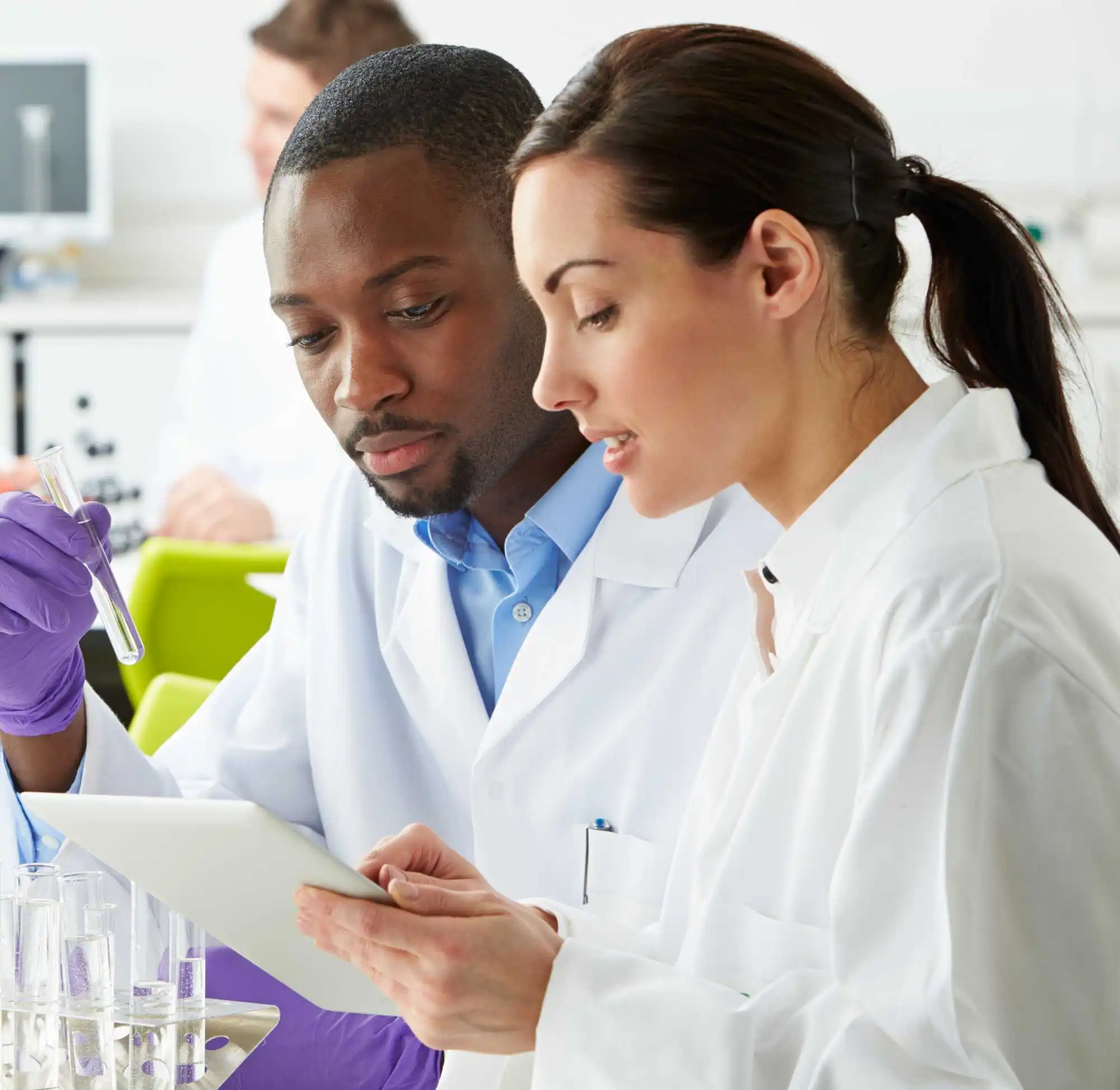
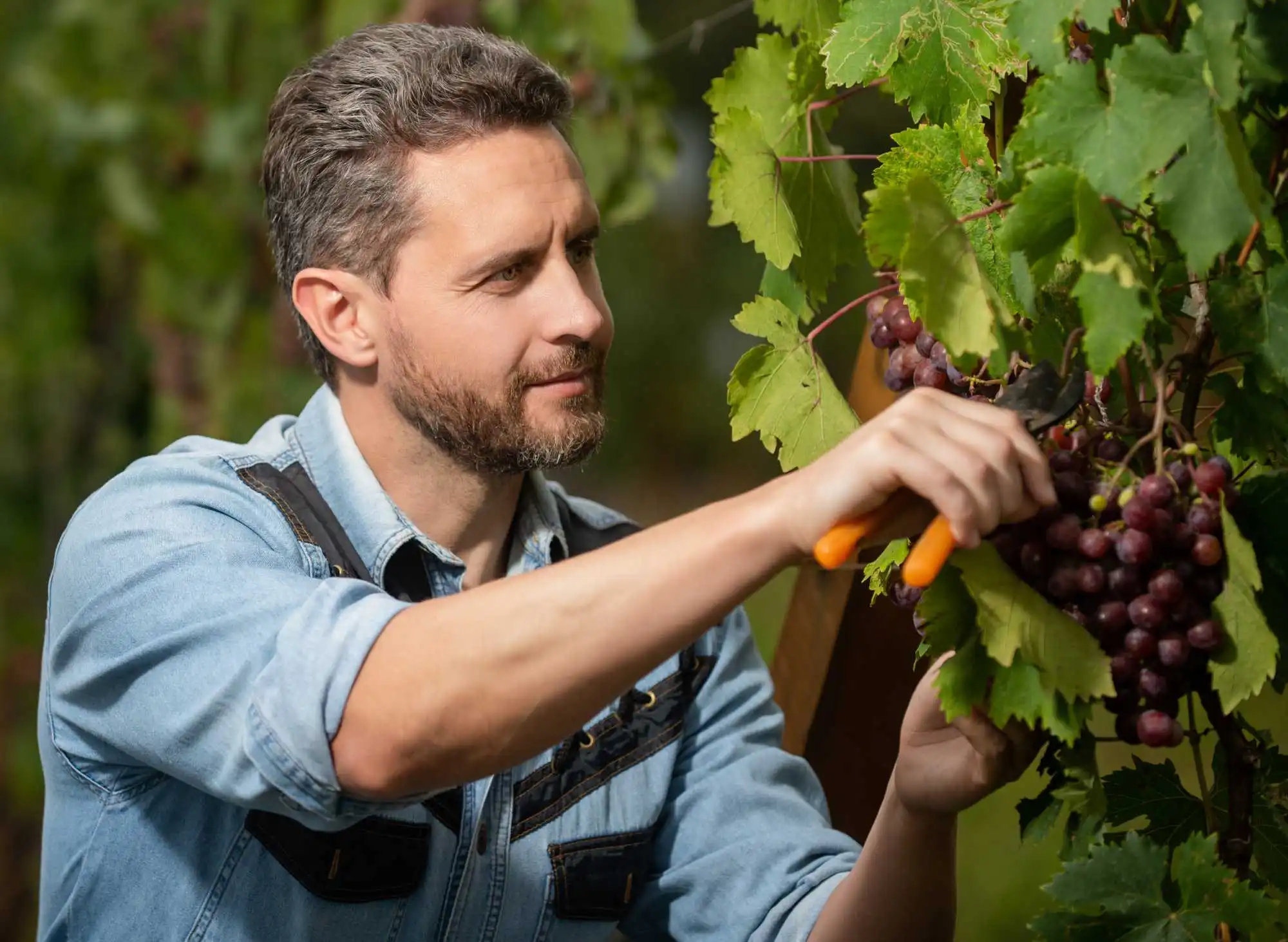