Improved Inspection Accuracy, Reduced Labor Costs
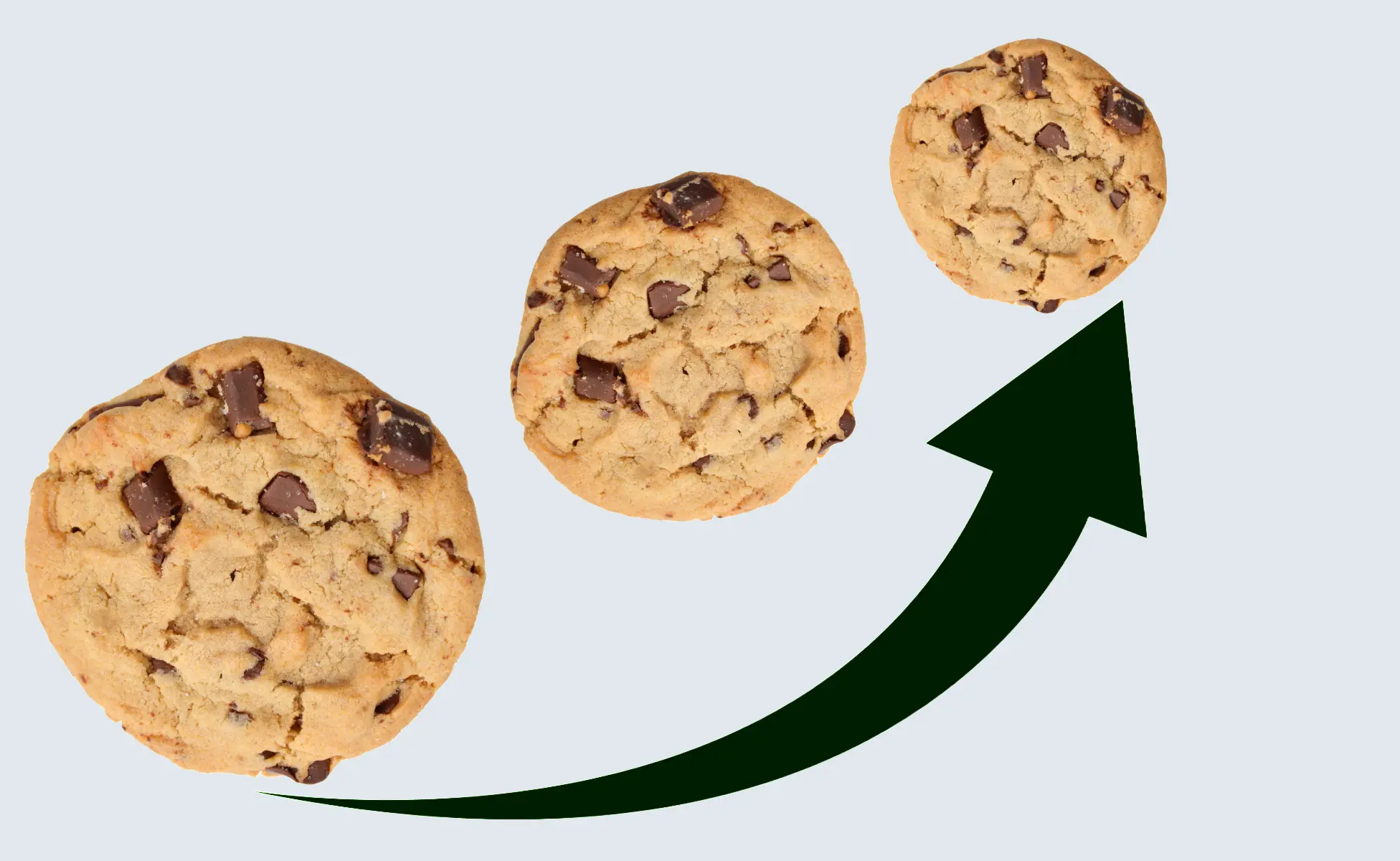
Table of Contents
Vision Inspection Introduces Objectivity to the Process
Being a product inspector is not the most glamorous job, but it is a vital responsibility within every baking operation. These individuals are essential for helping plant operators monitor the health and performance of their process, using the data collected directly from the line to make critical production decisions.
However, from the product inspector’s perspective, it is generally unexciting work. Standing for hours each day at the end of the production line, leaning over the conveyor line repeatedly to grab samples, and following repetitive steps to measure products for specific attributes (weight, bake color, moisture content, etc.) can be draining over the course of a shift. As a result, the product inspector position is notorious for having high turnover within a baking organization, which makes it difficult for companies to train new staff frequently while maintaining strong quality standards.
Additionally, it is common for product inspectors to select products that only appear within specifications rather than being completely random in their selection process. They may only grab from a few regions rather than selecting products across an entire line. These biases may change throughout a shift, making it nearly impossible for organizations to maintain accuracy across their quality assurance team.
Many bakeries have fortified product inspection processes with automated vision inspection technologies, like the Q-Bake Vision Inspection System from KPM Analytics. Automated vision inspection technologies collect and measure every product on the production line much faster and with better repeatability than a human product inspector on the line.
The flexibility of vision inspection technology makes it an attractive option to help baking companies control quality across many different baked product types. For instance, as shown in Figure 1, a cookie/biscuit manufacturer may prioritize the overall color and uniformity of their final products, while a bread bakery may value insights directly after dough shaping, through proofing, and after cooling to verify their production decisions.
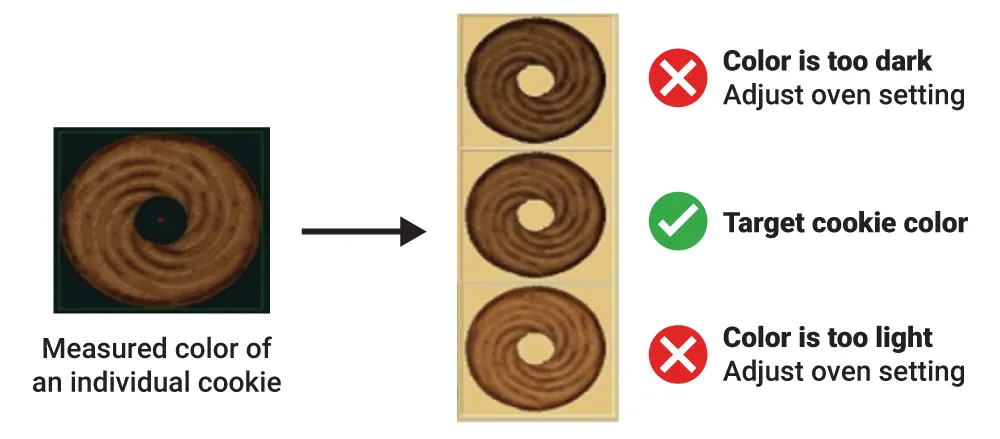
These applications can help determine if adjustments are needed on different production lines – or even different lanes within the same line – enabling 100% inspection of products, helping reduce errors and waste before they become more significant problems.
However, improved inspection accuracy is only one of many benefits bakeries can gain from automating their inspection process.
Case Example: Reduced Labor Costs Introduce a Major Return on Investment
One cookie manufacturer took a moment to calculate how much an investment in their product inspection team cost the company.
Factoring in the individual’s hourly rate of pay and benefits, each inspector for one production line costs the organization just around $100K per year (calculated by $15/hr day + benefits / 8 hours per shift / 2 shifts per day / 6 days per week, 48 operating weeks per year).
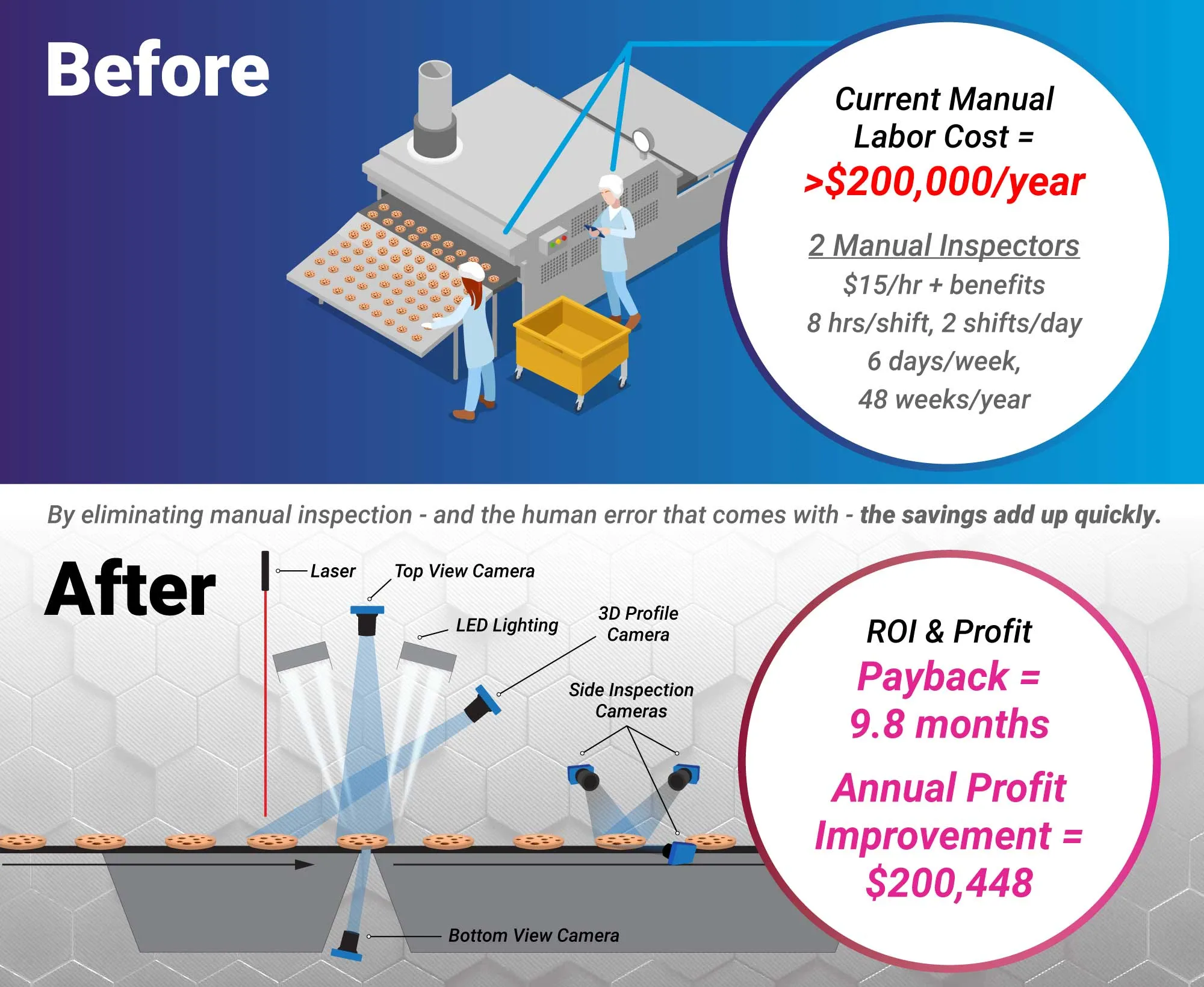
After vision inspection integration: By reducing their manual inspection team – which led to fewer errors, reduced waste, and other production benefits – the company generated an annual profit improvement of over $200K. This savings alone paid for the company’s vision inspection system in under one year.
Product Quality & Consistency Builds Stronger Brands
Baking brands have a solution to ensure all products maintain visual brand standards batch after batch with the help of automated vision inspection solutions. For more information on automated vision inspection technologies, contact us today!
Related Blog Posts
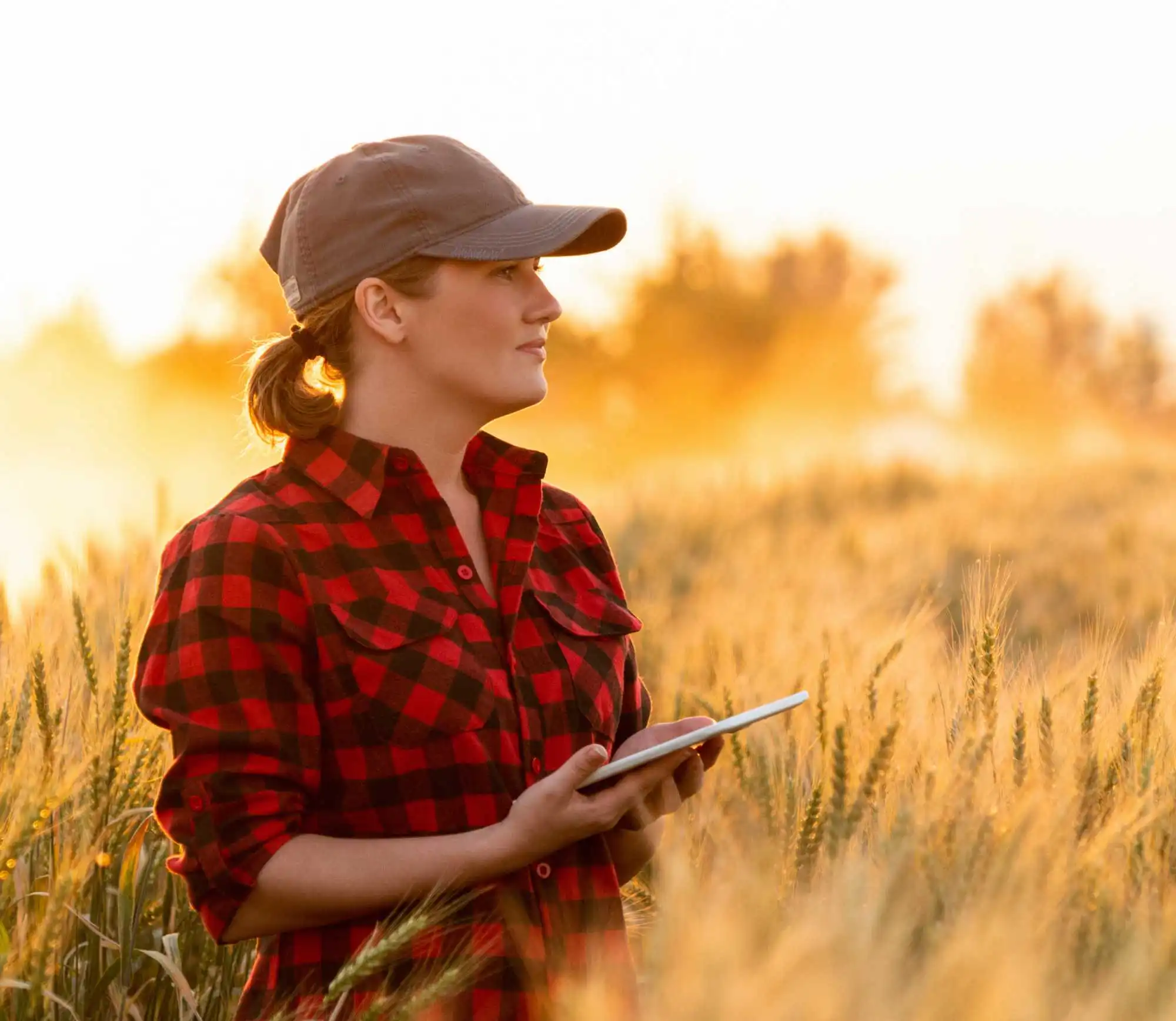
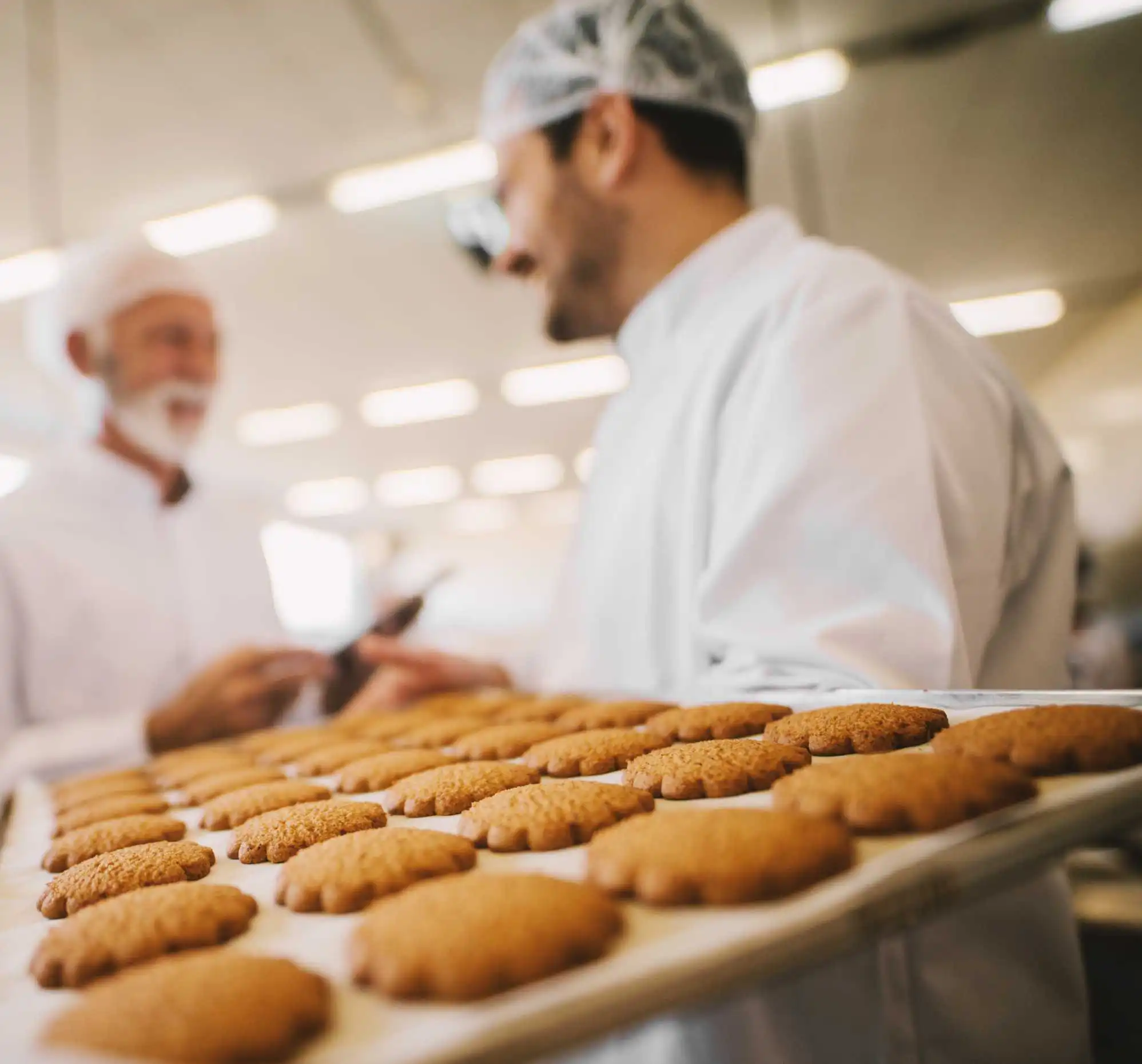
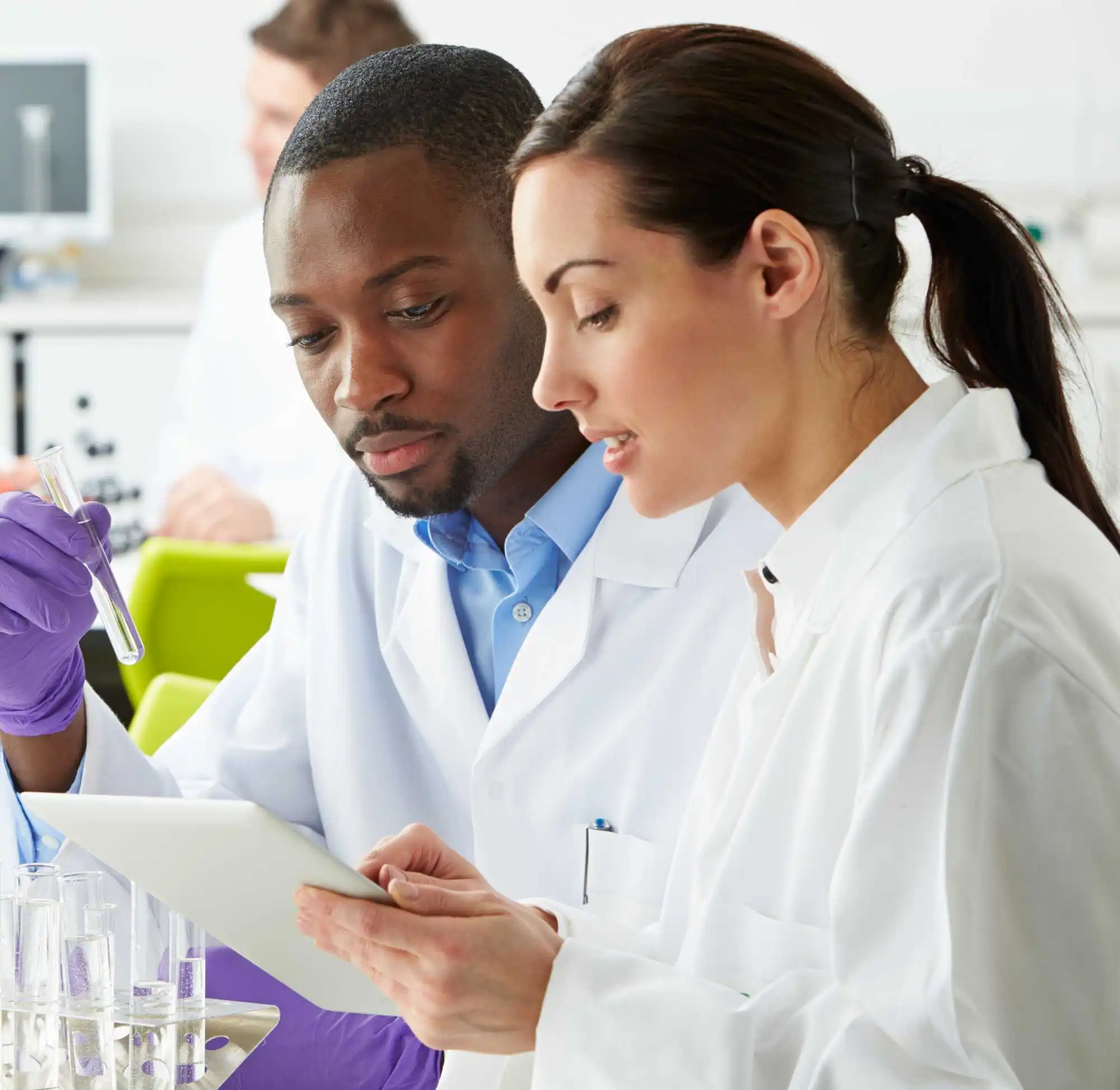
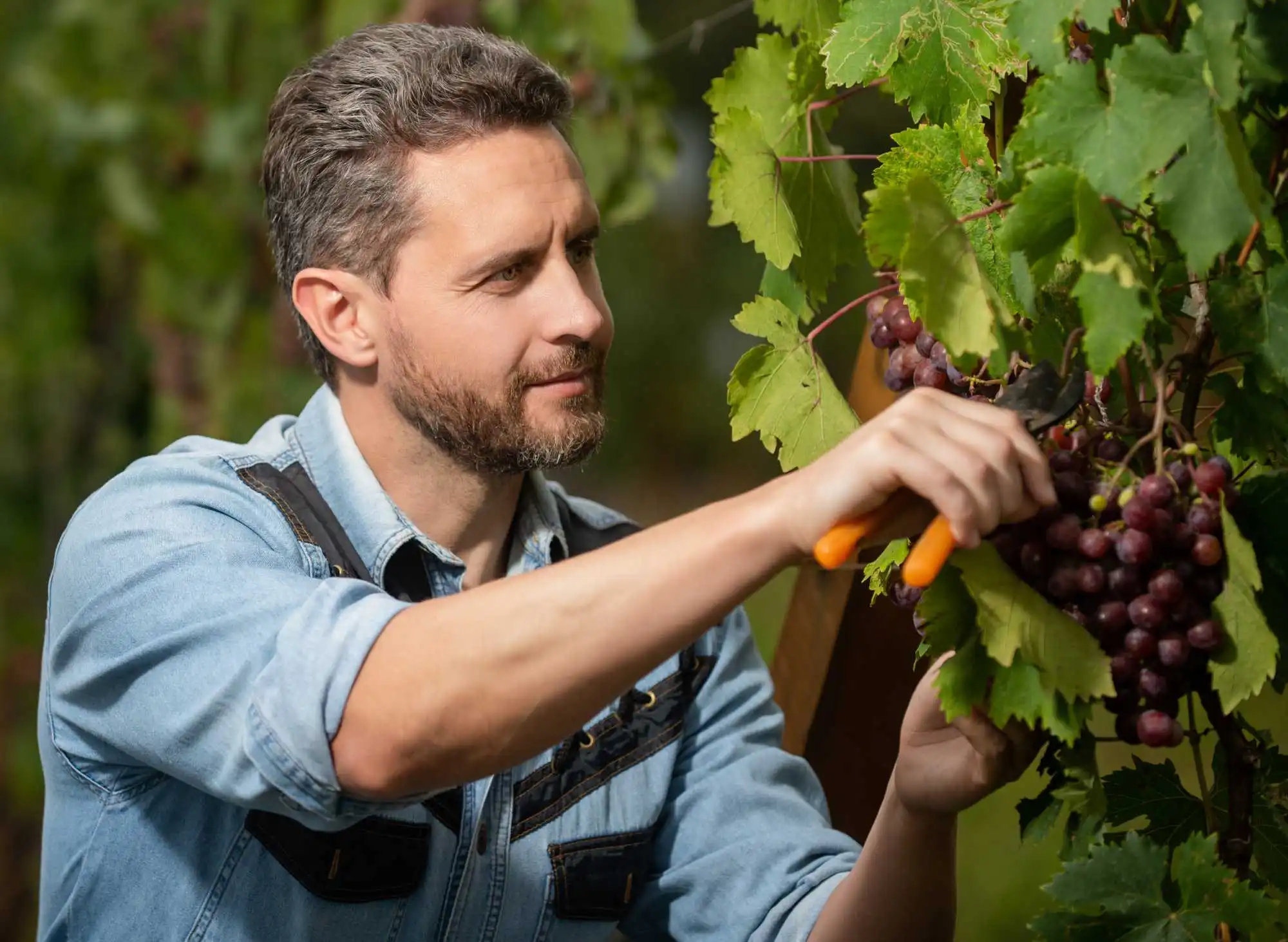