利用 AI 强化食品安全和质量
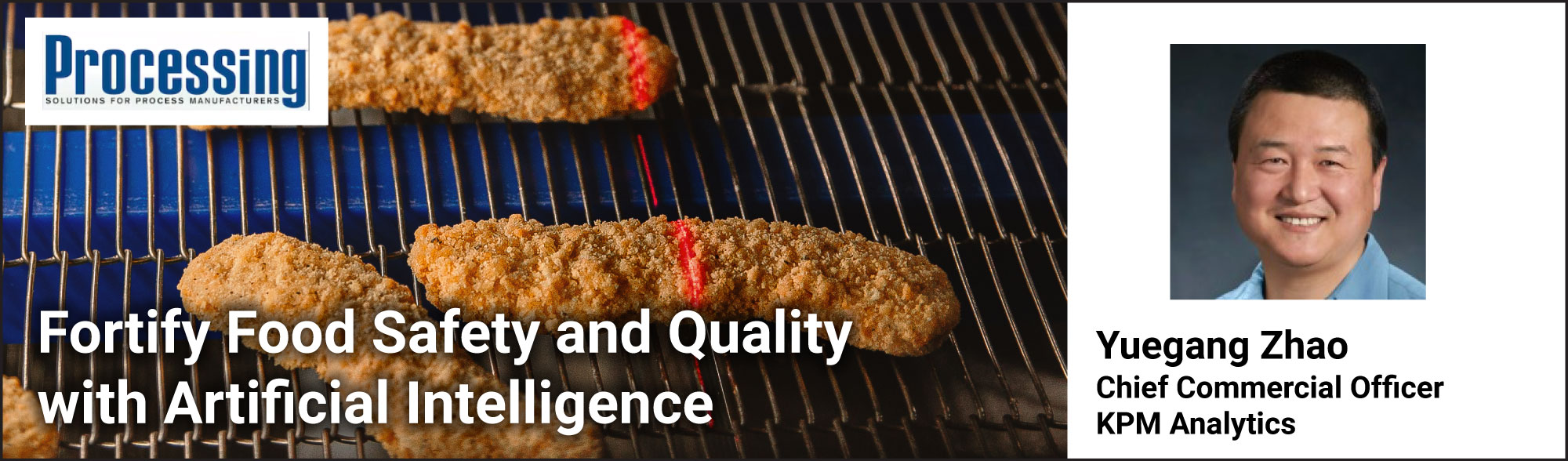
这篇文章最初发表在《加工杂志》上。 点击此处查看该出版物网站上的文章。
从裹面包屑的鸡肉饼到巧克力曲奇,近年来,当今食品加工设施的生产技术和吞吐速度发生了巨大变化。从原料进入工厂直到最终产品包装完毕,这种向更高的自动化程度和更少的人工参与的过渡就显而易见了。
尽管有这些新兴的生产方法,但许多食品加工商仍然严重依赖人工产品检查员作为最后一道防线来验证最终产品质量并检测可能导致代价高昂的产品召回的有害异物。常见的食品安全技术,例如擅长探测金属或骨头的X射线和金属探测器,很难与低密度或非金属异物(例如塑料、橡胶、木材和颜色与食品相似的物体)作斗争。
为了解决这些限制,食品加工行业越来越多地转向人工智能 (AI) 驱动的视觉检测系统。这些系统提供增强的检测能力和操作效率,可应对现代生产环境的挑战。
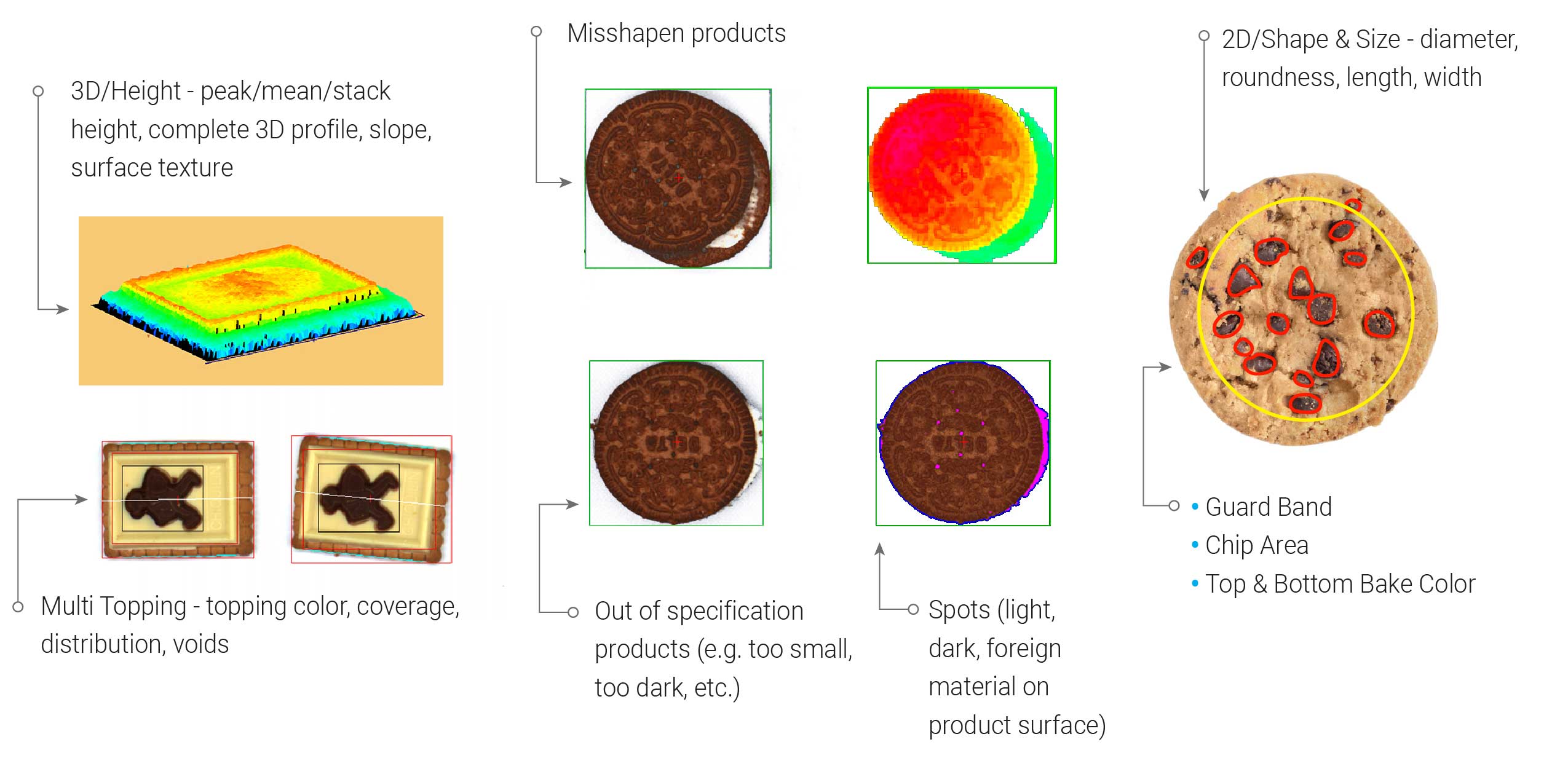
食品检验的新时代
在线视觉检测技术对食品行业来说并不是什么新鲜事物。几十年来,一些基于规则的视觉检测系统已成功应用于生产线。这些系统结合了高分辨率的二维和三维摄像头,分析产品的各个侧面,以获得预编程的视觉特征,包括产品的底部。从切好的牛排的整体尺寸、形状、颜色和大理石花纹到芝麻籽汉堡包上的种子分布,基于规则的视觉系统都能有效检测到有限的产品细节,而这些细节在全线运行时几乎是不可能的。
在线视觉系统还可以与拒绝机制集成,以自动从工艺流中移除不合格产品或提醒操作员采取行动。
随着对这些系统的需求增加,基于规则的视觉系统正处于技术极限状态。生产商过去对检查少数产品方面感到满意;现在,他们对更多方面感兴趣。例如,回到汉堡包的例子,许多快餐店(QSR)现在更喜欢产品表面始终有光泽的面包。但是,这种光泽会影响视觉系统的色彩测量。公司可以通过正确的照明示意图、软件和相机设置来捕捉这种传统上难以测量的产品特征。
这些不断增长的需求促使技术提供商探索人工智能,以简化产品检测系统的测量模型构建。对产品规格和功能进行自动机器学习可显著降低系统复杂性并简化产品设置,从而帮助公司在质量和食品安全控制方面达到更高的水平。
通过对产品表面进行更深入的分析,人工智能检测不仅限于色度计、X 射线和金属探测系统。人工智能经过训练,可以检测人类所能看到的以及其他内容。
人工智能支持复杂的测量功能
举个例子,让我们以一家冷冻披萨制造商为例,该制造商面临着生产稳定的产品的挑战。大多数披萨厂都有多个阶段,当产品通过输送机时,配料会自动应用到产品上。对于人类操作员来说,这种快速且有时是混乱的过程往往难以精确控制。
每个披萨都有多种配料、质地和颜色。通过基于规则的愿景,操作员必须对披萨上每种食材的单独测量值进行编程,并将其分层到整体产品测量值中。根据披萨的类型,这些测量可能需要巨大的计算能力和测量卷积。
现在,借助人工智能检测,披萨操作员可以训练软件,立即以极高的精度检查整个披萨及其所有复杂性。
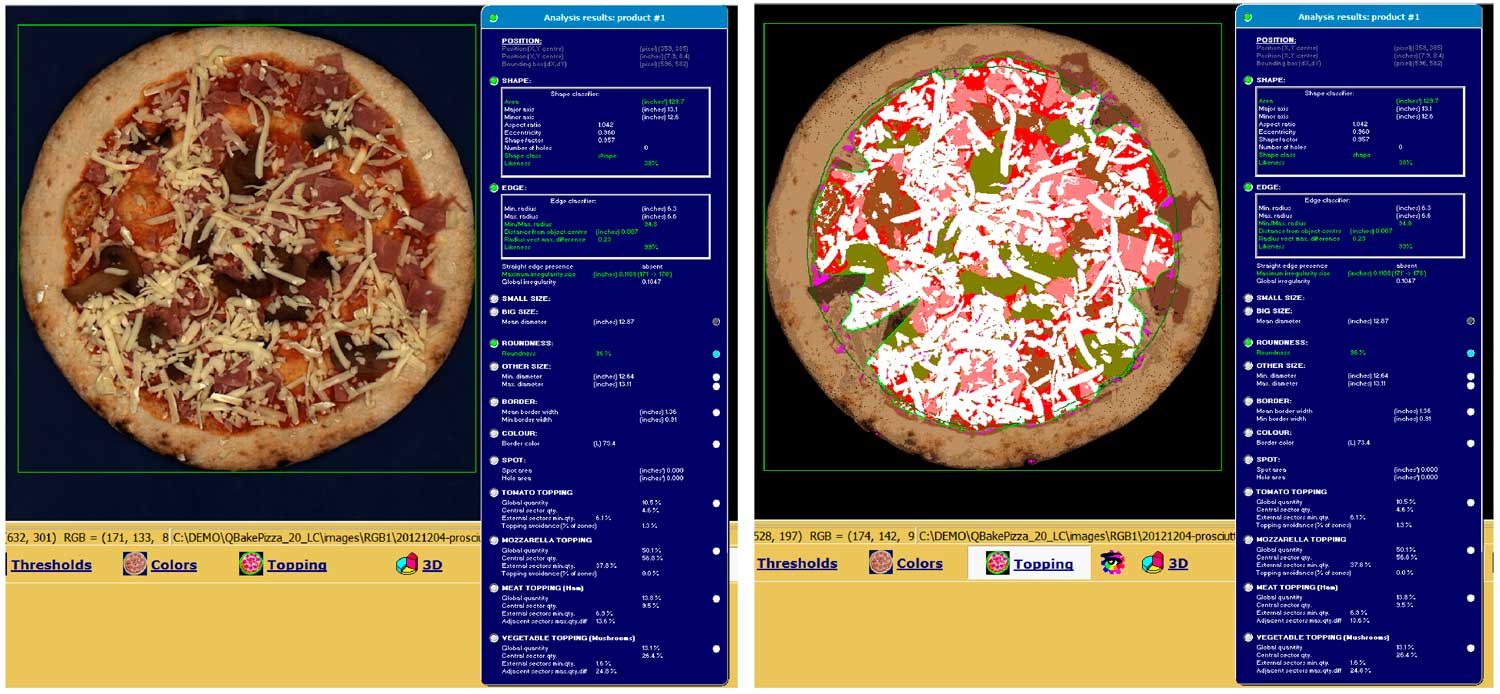
同样,人工智能驱动的检测系统也知道产品何时未达到理想的规格。例如,一些冷冻晚餐制造商使用人工智能系统来确保将食品原料直接输送到正确的包装组件中,确定是否缺少任何产品(例如瑞典肉丸冷冻餐中的肉丸)或验证产品包装。
人工智能在食品安全领域的建构案例
长期以来,食品加工公司在留住和培训现场产品检查员方面一直面临挑战,尽管这些职位对于确保质量和食品安全至关重要。但是,风险很高——由于未被发现的有害异物而召回一次产品就可能造成严重的经济损失,并损害品牌在市场上的声誉。
食品行业产品召回的财务影响可能是惊人的。根据食品营销研究所和消费品牌协会的研究,平均召回成本从1000万美元到3000万美元不等。这些成本包括通知消费者和零售商、从货架上移除产品、处置受污染的物品以及管理由此产生的公共关系挑战。
食品加工公司越来越多地转向人工智能驱动的检查系统来降低这些风险。通过投资先进的系统来检测潜在危险,公司可以保护其运营,保护客户并降低代价高昂的召回可能性。
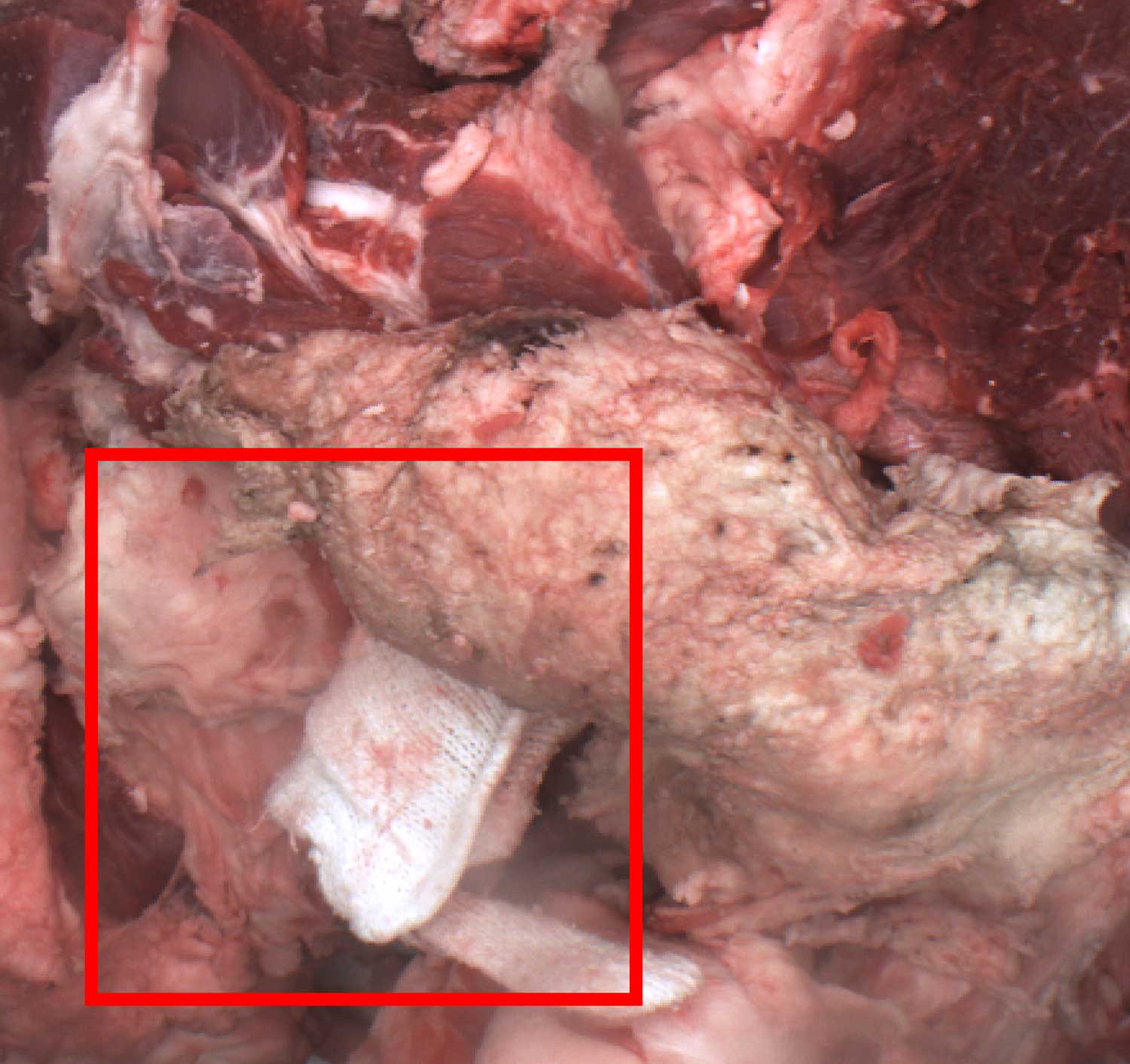
此外,对于卫生环境严格的肉类、家禽和海鲜加工厂,人工智能检测系统可以满足冲洗要求(IP69K、NEMA-4X 等)。例如,加工牛肉切片的公司使用这些卫生检查系统通过X射线和金属探测器识别无法检测到的异物。由于牛肉切边很少是均匀或一致的,因此基于规则的视觉系统很难从有害物质中分辨出优质产品。但是,人工智能系统可以立即将其在加工线上分析的所有内容分开,并立即识别出其认为不符合验收标准的材料。
在异物进入后期处理阶段之前对其进行检测,可以在系统的使用寿命内为公司节省数百万美元。这不仅可以快速获得投资回报,还有助于维护消费者对品牌的信心。
人工智能为植物通常陷入困境的地方提供支持
人工智能将继续成为全球争论激烈的话题,尤其是其对在各个行业和职责中取代人类劳动的影响。但是,在食品行业,留住关键质量保证职位的劳动力一直很困难。
人工智能检测技术通过将100%的客观性应用于其检查过程来有效地满足这些需求——这是人工操作员无法实现的。公司不必花费大量时间、金钱和精力对员工进行这些重要而又平凡的重复性任务的培训,而是可以在工厂的其他地方赋予这些员工更有意义的责任。
此外,部署人工智能视觉检测系统的一个基本原则是必须有人参与这些系统的培训和维护。在人类专业知识的指导下,主要通过监督学习方法,人工智能应用程序可以取得最佳成功。因此,人工智能永远无法完全取代食品生产中的人为因素;相反,它将使工厂在不牺牲质量或食品安全努力的情况下有效满足不断增长的需求。随着人工智能技术每天都在快速发展,它将更广泛地应用于食品加工行业,以确保以更高的吞吐量和更低的成本获得更安全、更优质的食品。
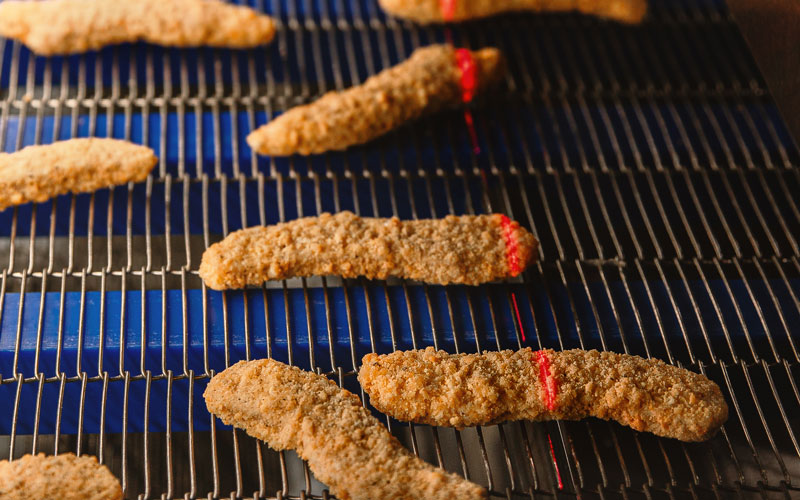
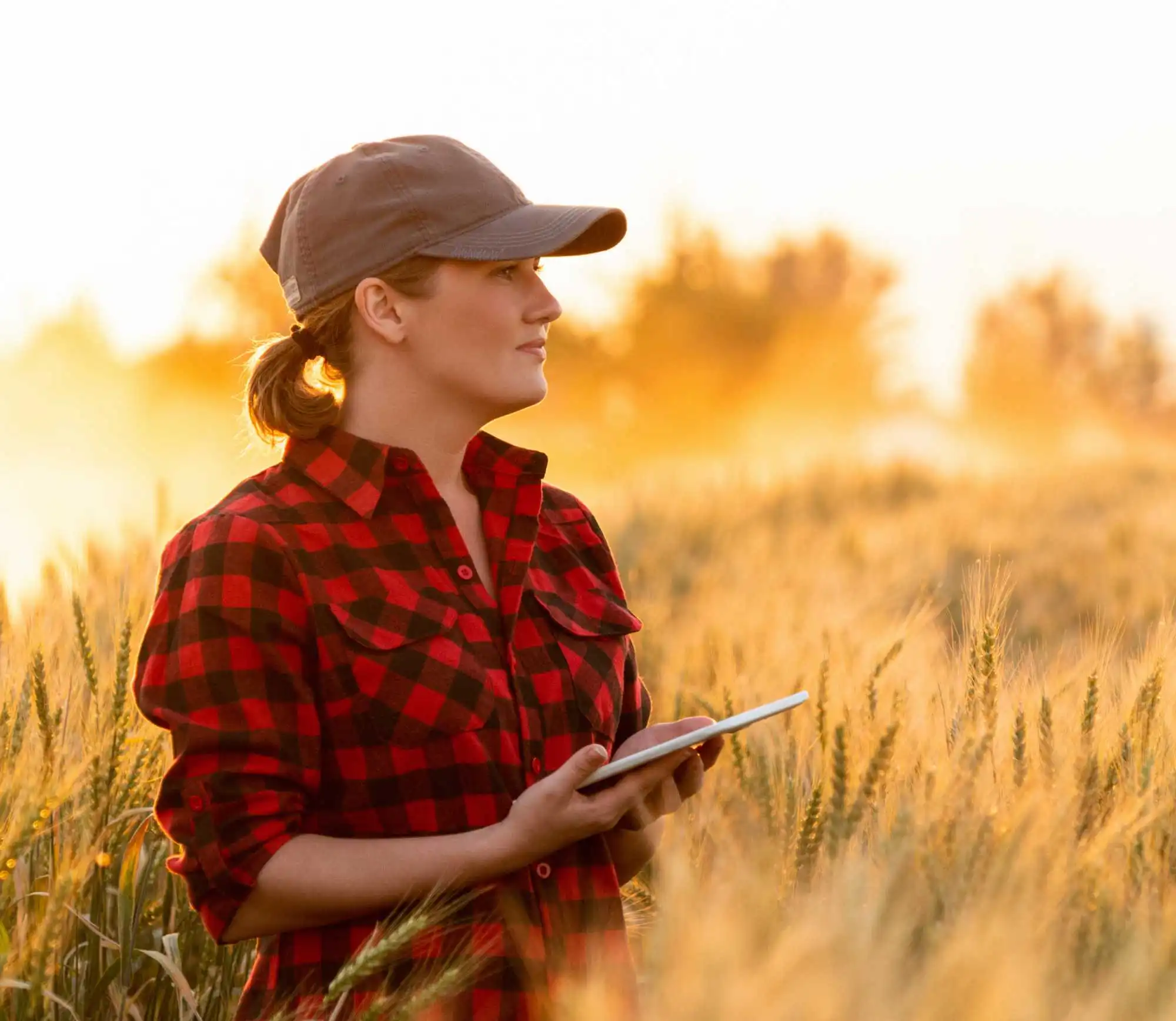
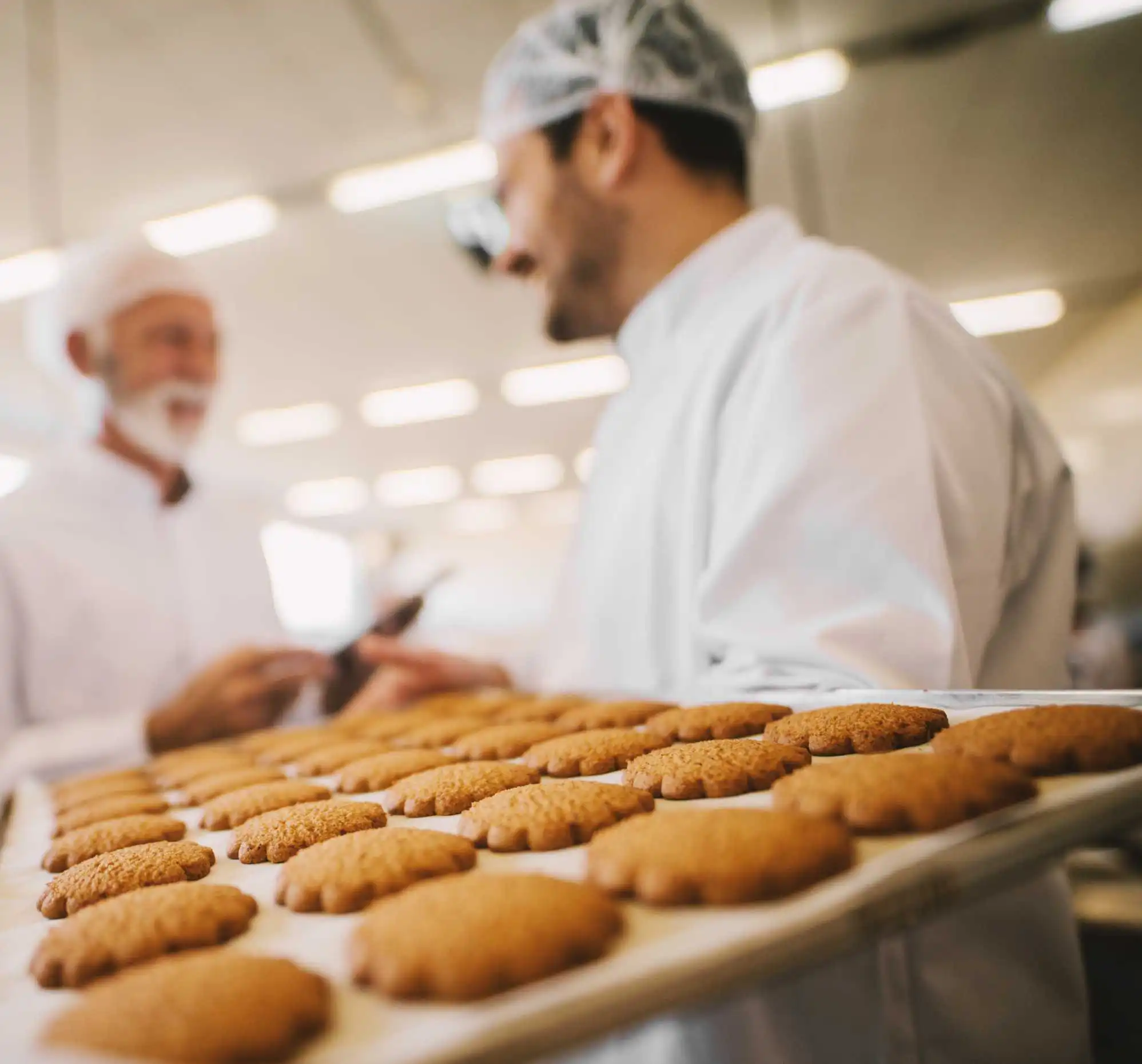
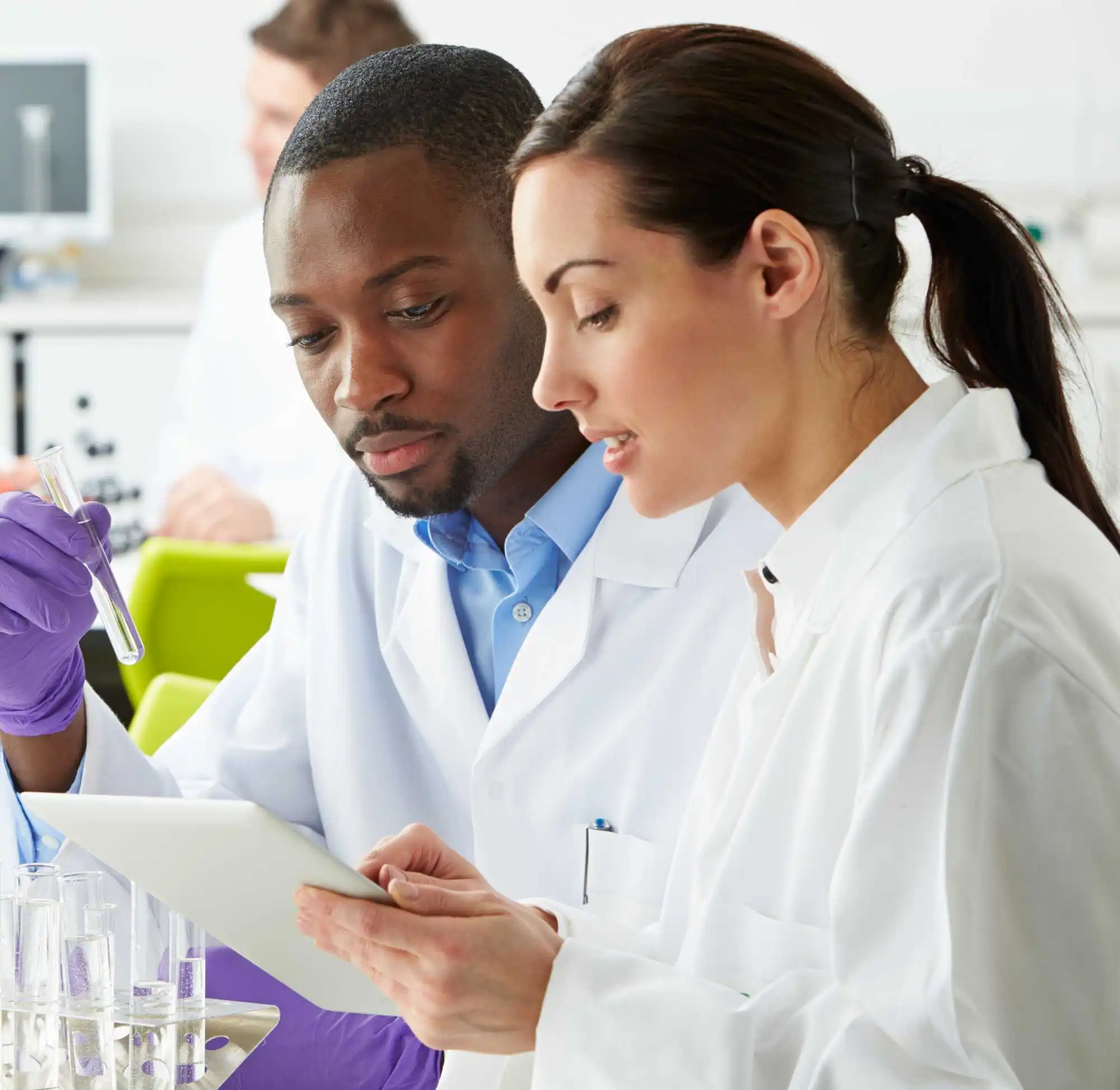
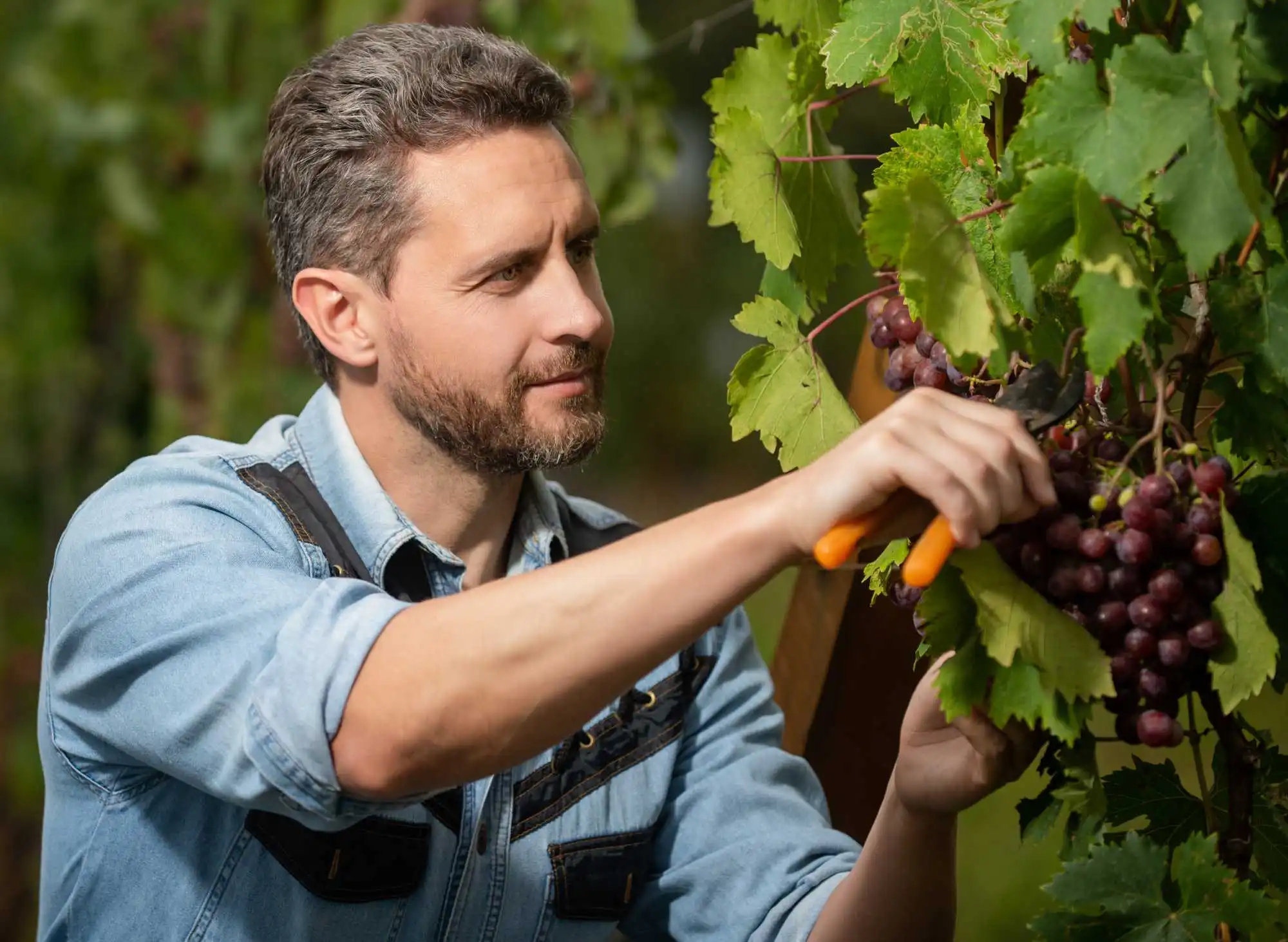