Feed, Forage, & Pet Food
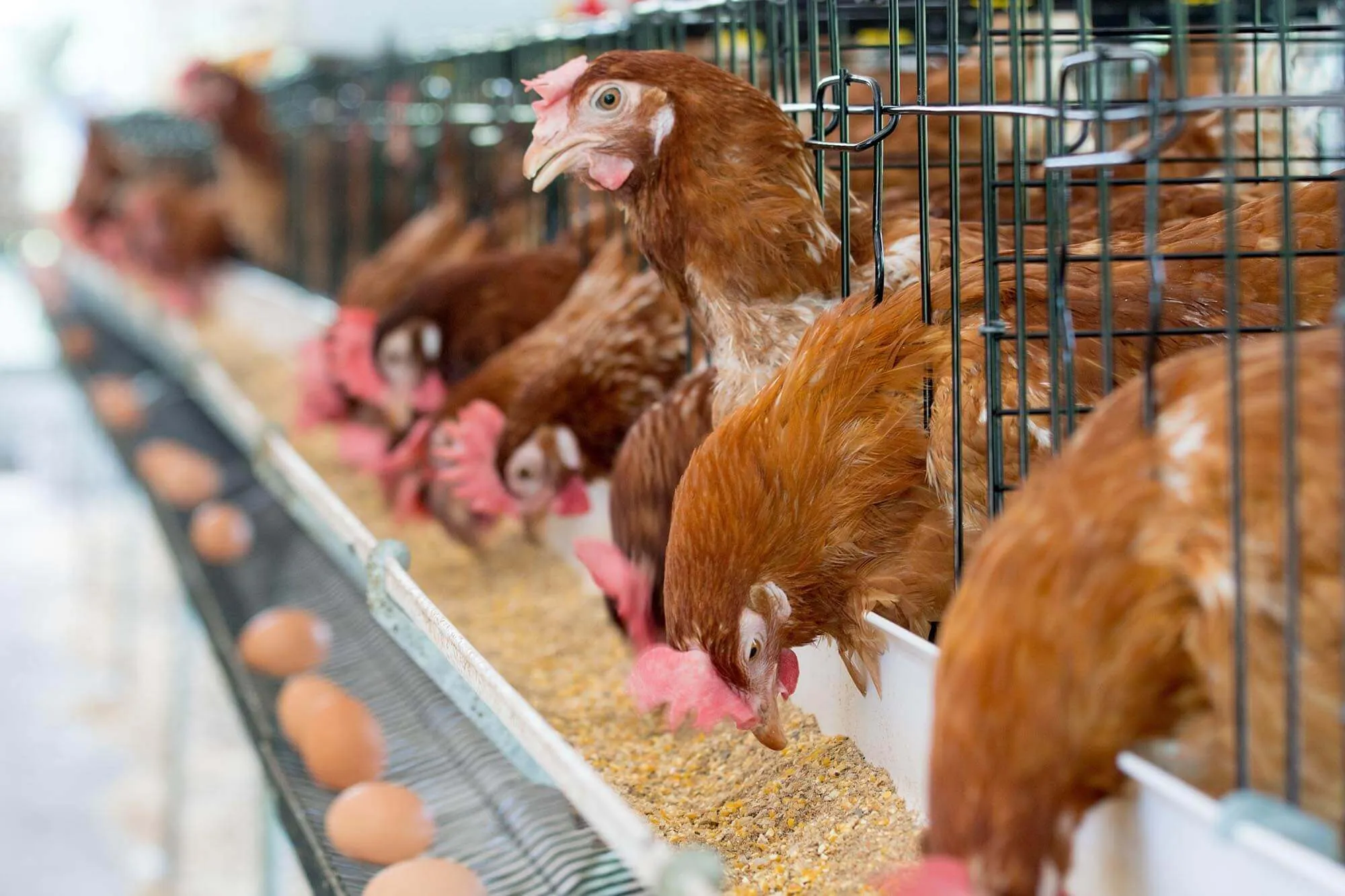
The animal feed and feed ingredient industry produce over 1 billion tonnes of compound feed annually. Cows, poultry, pigs, sheep, fish and other livestock convert this feed into animal protein and milk, providing over 1/3 of the protein consumed by a growing human population.
While regional consumption varies and diets change over time, animal protein and dairy products represent a significant source of protein that nourishes a hungry and growing global community. To support the production of this important food source, a diversified collection of agricultural growers and industrial processors generate the raw materials used to feed poultry, ruminants, swine, aquaculture and other livestock.
The global compound feed market alone is projected to grow from USD 510.42 billion in 2021 to USD 709.62 billion in 2028.* When combined with the agricultural and ingredient processors, these industries represent a major part our food production with a truly global impact.
As with other industries, livestock production has become increasingly specialized and optimized, with improved animal breeds, production practices, and nutritional programs. Animal producers require precise nutritional profiles to maximize weight gain or milk production. With the raw ingredients primarily commodities, efficient production is often the difference between profitability or a loss.
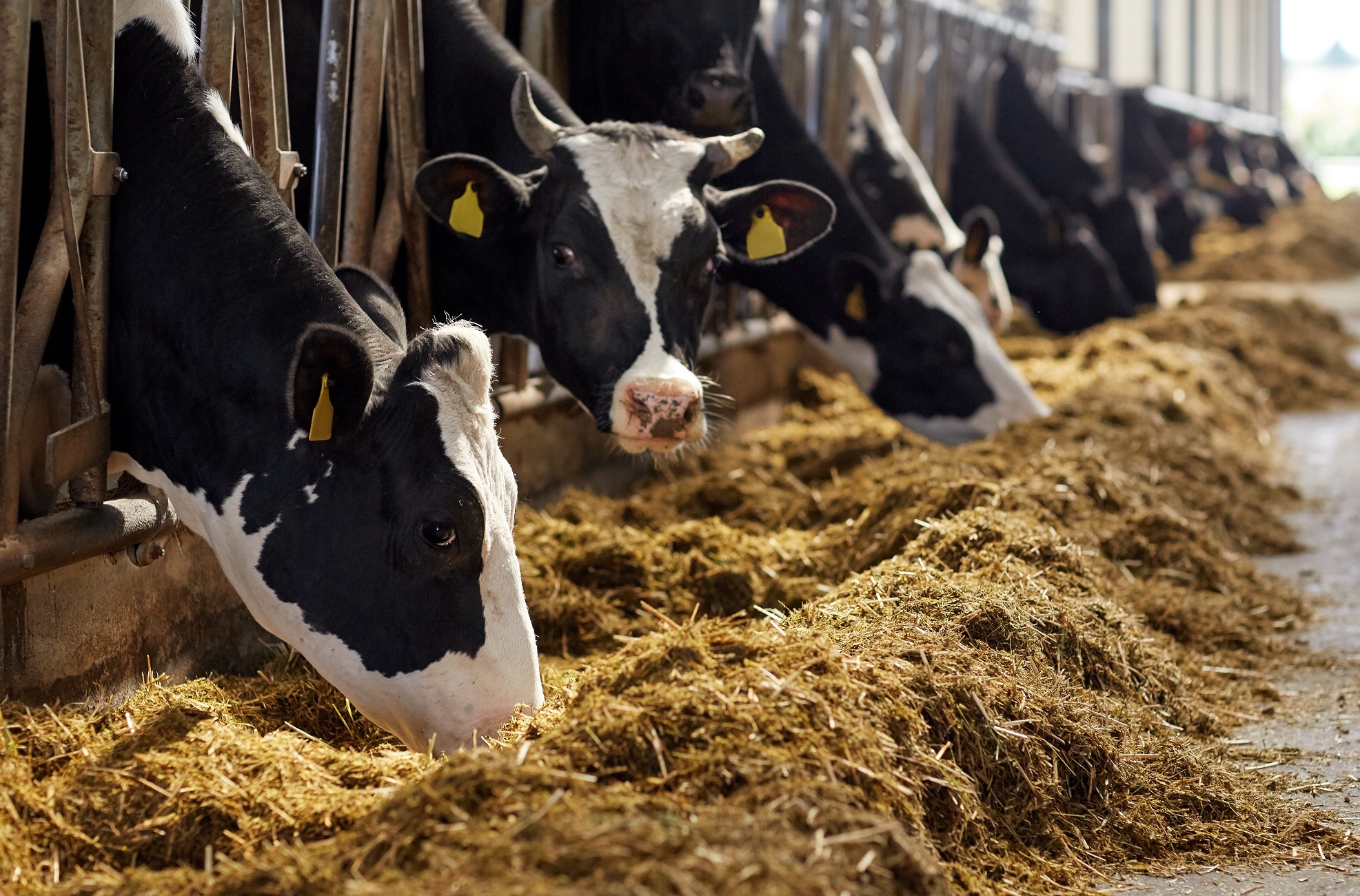
Compound feeds are produced from various ingredients, including animal meals or agricultural products such as grains, forages, oilseeds, and by-products from other manufacturing processes such as vegetable oil production or biofuel production. Additionally, many new food processing by-products such as beet pulp, vegetable pomace, and bakery products are used as a significant component in feed mixtures. These products can have a wide range of nutritional quality, making consistent feed production challenging. Providing a consistent product and nutritional guarantees can add significant value to these ingredients.
Feed mills combine these ingredients, such as poultry meal, meat and bone meal, soybean meal, corn, rice, etc. in a proper ration to get the desired nutrition content. Depending on the product, these feeds are then extruded or otherwise processed into the complete compound feed tailored for the animal species and life stage.
Fast, accurate analysis is critical for finished feed and feed ingredient manufacturers to optimize their process and ensure quality. Optimizing the process will save the plant time and money and provide very rapid payback. Near-Infrared (NIR) analysis is a proven technique designed to provide fast, accurate, and reliable results for the feed and feed ingredients industry.
KPM Analytics has deep knowledge and years of experience providing feed and feed ingredient producers with rapid analysis at-line for quality control. NIR analysis is ideal for every step in the feed manufacturing process, including:
- incoming ingredient testing to verify nutritional specifications and support out-of-spec claims
- raw material testing to guide proper ration supplementation
- raw material testing to control meal formulation
- raw material testing to optimize least cost formulation
- monitoring and controlling mixers and optimizing the addition of liquid fat
- monitoring and controlling moisture levels in extruders and dryers
- verifying production batch values and optimizing fat spraying on pellets
- verifying and documenting finished feed label claims
Depending on the product and application, an at-line or an in-line analyzer might be appropriate. In general, at-line analysis enables technologies and sampling methods which support the analysis of more numerous and difficult constituents, while in-line analyzers are generally limited to moisture and possibly fat.
SpectraStar NIR analyzers with Aunir Ingot calibrations deliver complete proximate analysis of over 100 feeds and feed ingredients. In less than a minute, our NIR systems provide simultaneous results for moisture, protein, fat, fiber, starch, ash, and other parameters. Typical measuring points are during the ingredient processing, incoming raw material streams, at the mixer and pre- or post-dryer. SpectraStar XT analyzers detect inferior raw materials, optimize the use of raw ingredients and verify feed label claims to optimize production and maximize profits for processors and feed manufacturers.
MCT Process analyzers on-line enable feed producers to tightly control moisture levels in the finished product, saving energy and raw material costs.
* Fortune Business Insights
Additional Reading
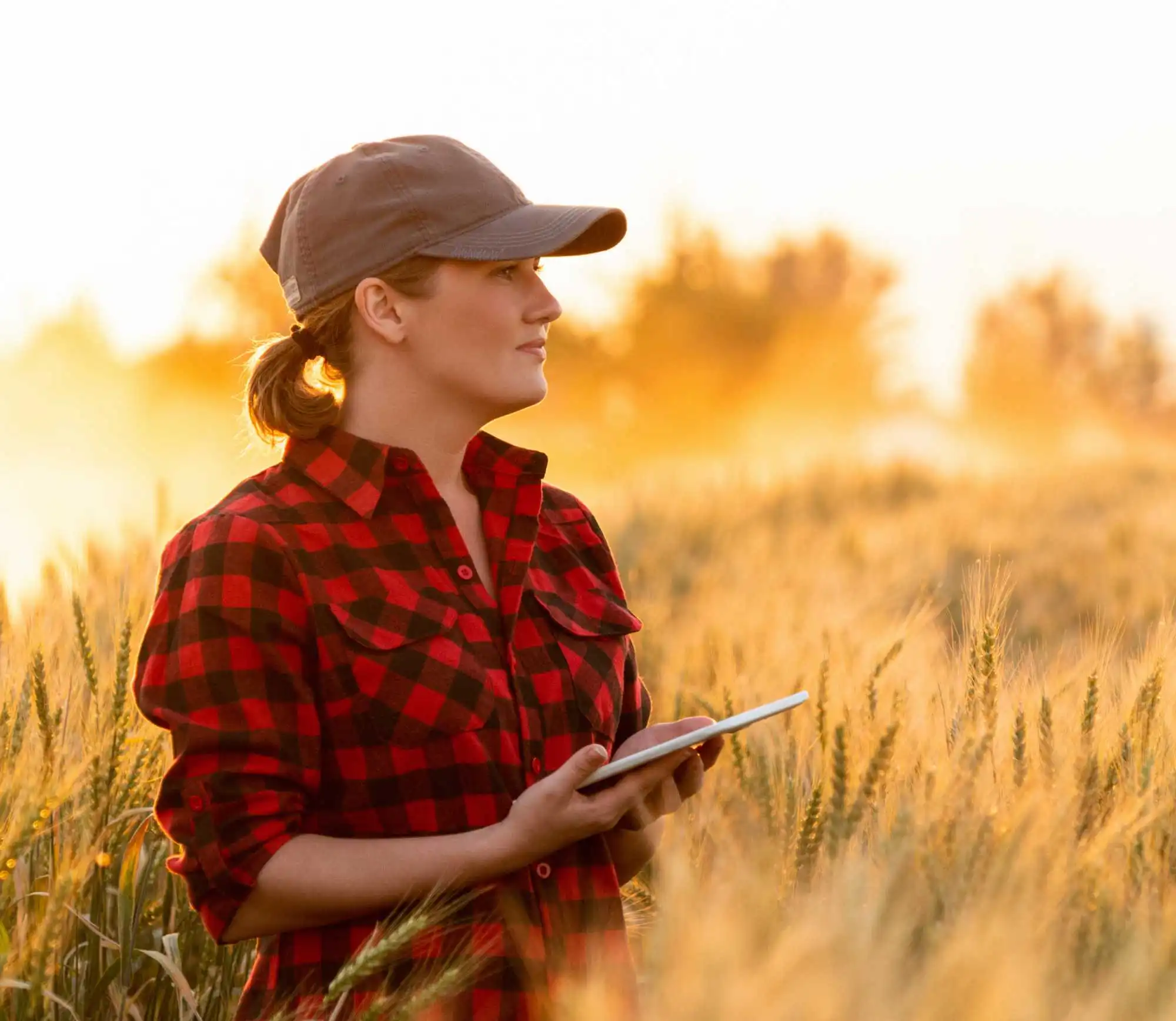
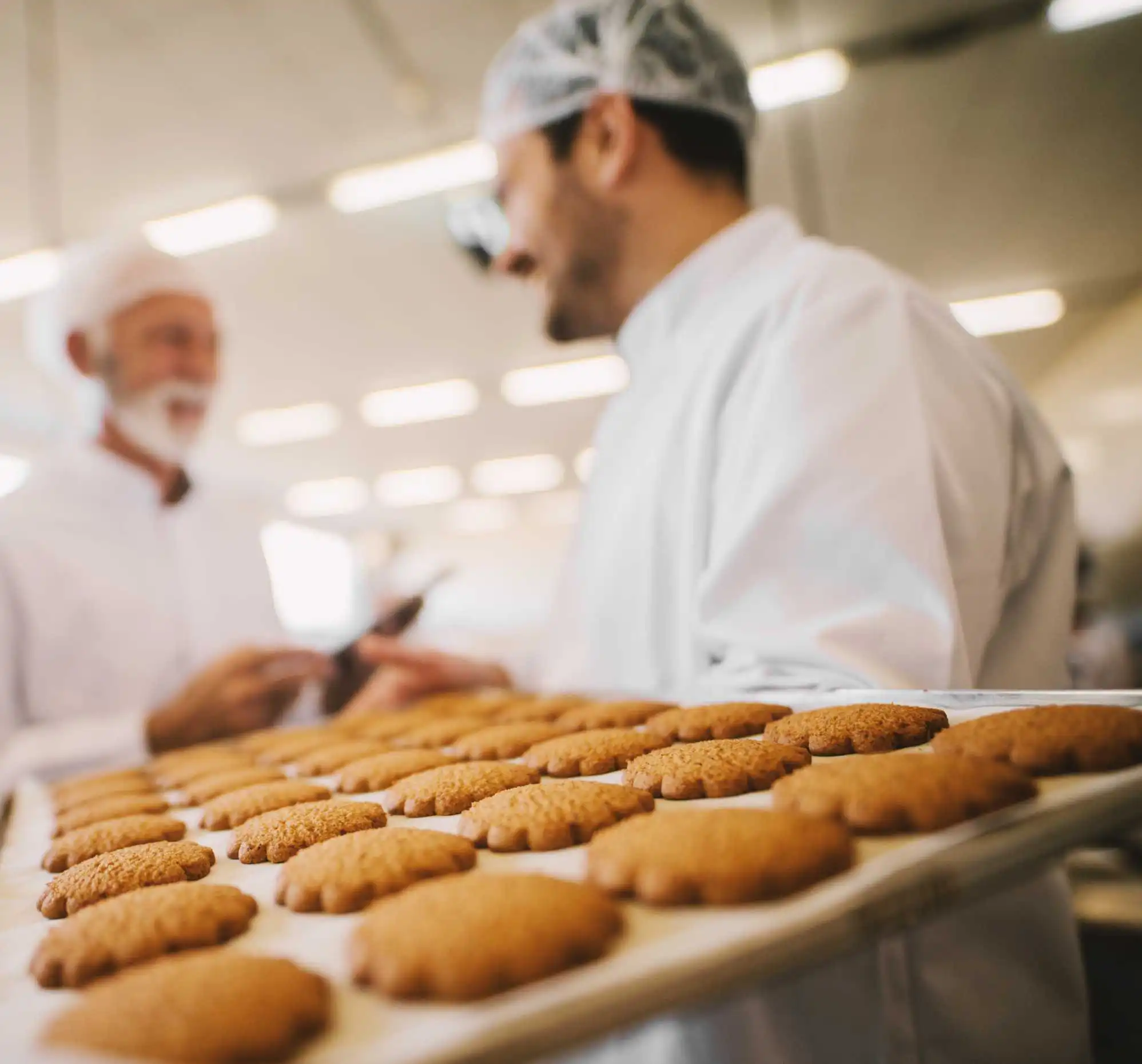
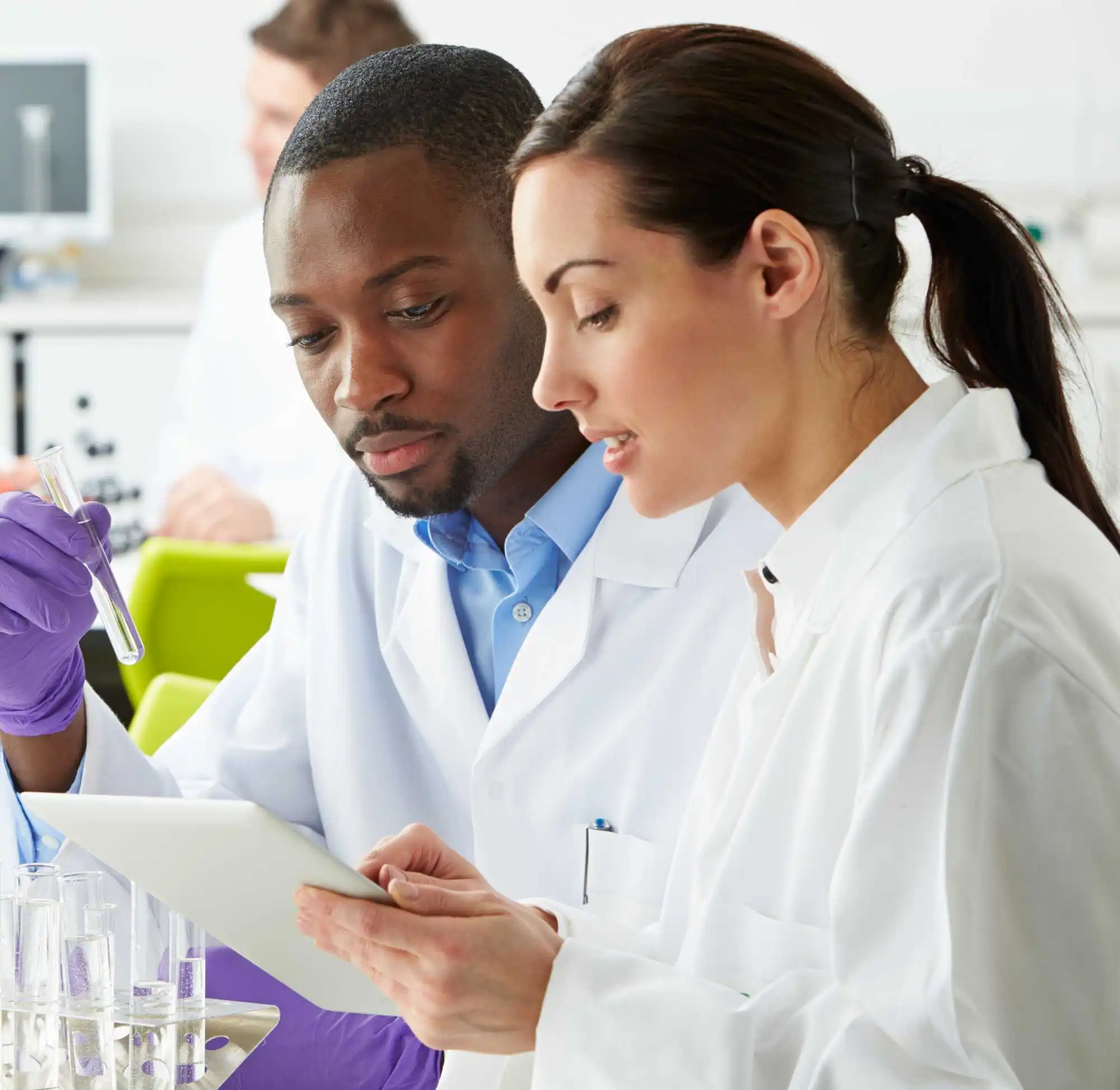
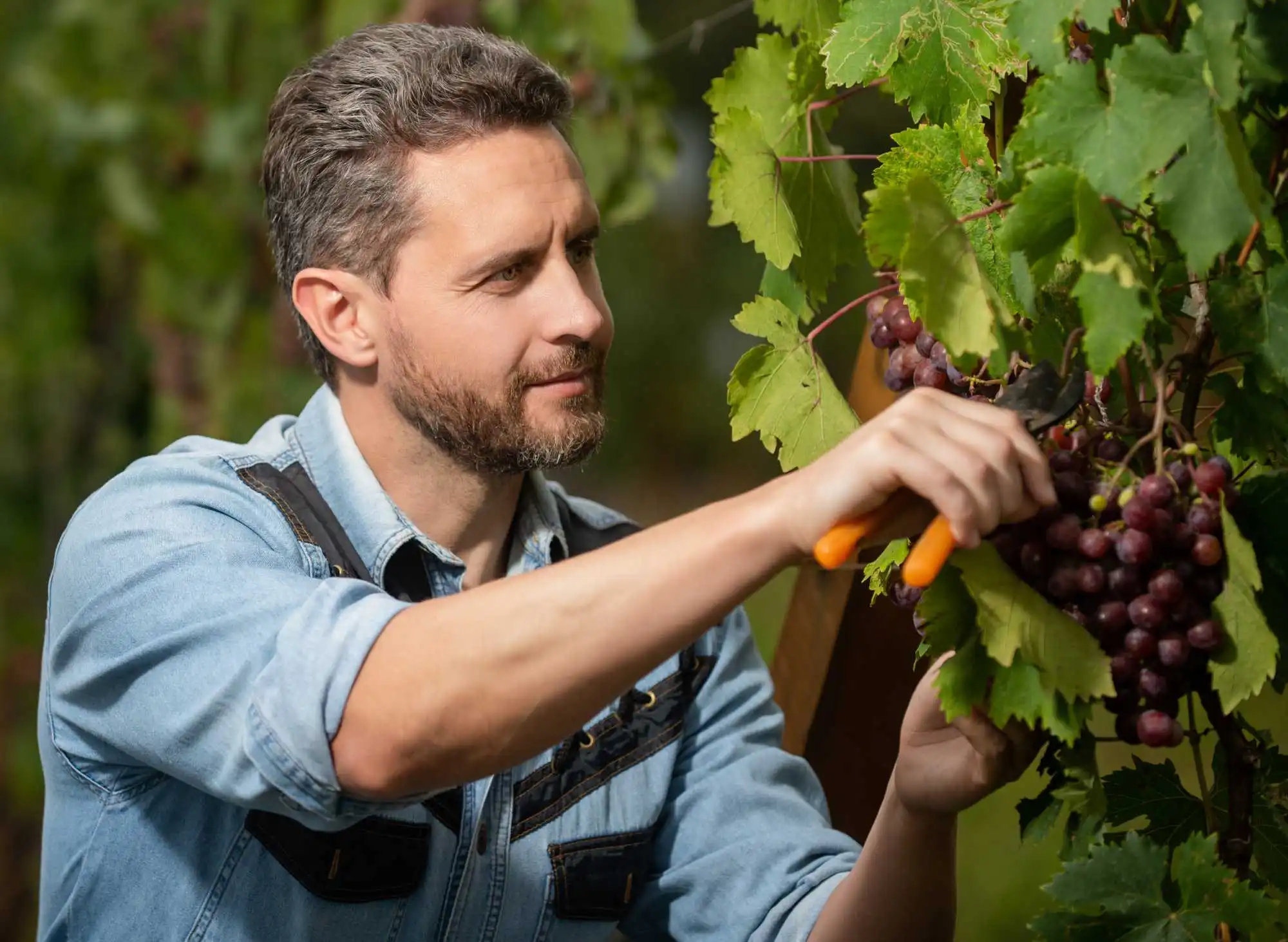